機械設計
出自 MBA智库百科(https://wiki.mbalib.com/)
機械設計(Machine Design)
目錄[隱藏] |
什麼是機械設計[1]
機械設計是根據使用要求對機械的工作原理、結構、運動方式、力和能量的傳遞方式、各個零件的材料和形狀尺寸、潤滑方法等進行構思、分析和計算,並將其轉化為具體的描述以作為製造依據的工作過程。
機械設計的發展階段[2]
設計是人們根據預定目標來產生滿足要求的信息的一種活動。信息的表達形式有圖形、文字、數據、符號等。技術是人類改造世界所採用的手段,是人的因素(知識、能力)與物化因素(工具、設備)的統一。設計技術是指從事設計活動所形成的作業程式、方法和技能,以及所用的工具和設備。根據設計技術的特征,可以將機械設計技術的發展分為5個階段。
1.直覺設計(遠古~1500年)
自人類開始製造工具,就有了設計活動。在古代,設計技術和製造技術體現在同一工匠個體上。他們或是從自然現象得到啟示,或是憑藉長期勞動所獲得的直觀感覺來設計和製作產品。
2.經驗設計(1501~1849年)
工匠開始利用力學原理組成各種裝置時,簡單工具逐漸向傳統機械發展。18世紀中期發生的第一次產業革命,使機械技術出現了設計與製造的分工。19世紀初,機械學從力學中獨立出來。19世紀後期,機械工程學逐漸成為一門獨立學科。機械學是機械工程學的理論基礎。由於當時的機械製造尚未形成一個學科體系,所以機械學可作為機械工程學的簡稱。當時的設計技術主要體現在機械學所研究的基本機構和基礎零件之中。設計主要是依靠設計者個人的才能和經驗,其局限性和隨意陛很大。
3.半經驗設計(1850~1949年)
1851年第一屆世界博覽會後,出現了大量複雜的機械產品。19世紀中期發生的第二次產業革命,使設計技術在理論和實踐上都有明顯提高。德國出版《理論運動學》,表明人們對設計的認識第一次從特性上升到個性。20世紀初出現的圖樣設計法,使成本大大降低。20世紀初開始了有組織的標準化活動,提高了設計的效率和質量。人們通過對關鍵零、部件的試驗和對各種專業產品設計質量的研究,減少了設計的盲目性。但是,該階段還未將設計本身作為一門學科來研究,設計還存在較大的經驗性和局限性。
4.半自動設計(1950~1989年)
該階段顯著特點是對設計工具的革新和對設計方法的深入研究。20世紀50年代電子電腦用於科學計算,60年代出現了電腦自動繪圖,1970年美國推出CAD系統,1971年日本出版了《設計工程學叢書》,1977年德國出版了《設計學》,這表明人們對設計的認識再次從特性上升到共性。20世紀80年代,電腦實現了信息處理自動化,設計者主要從事決策工作,且往往需要群體合作來完成設計。該階段逐漸形成了機械設計工程學。
5.自動化設計(1990年以來)
20世紀90年代,形成了建立在決策自動化基礎上的電腦集成製造系統(CIMS)。決策自動化本質上是對知識處理和使用的自動化。在該階段,設計過程中的大量一般性決策及信息處理可以由電腦完成,設計者可以僅作關鍵性決策。採用虛擬現實技術設計的波音777飛機,就是世界上第一架無圖樣、無樣機升空的飛機。
機械設計的模式[1]
機械設計是規劃和設計實現預期功能的新機械或改造原有機械的性能,其大體可分為以下幾種模式。
- 新型設計(開發性設計):應用成熟的科學技術或經過實驗證明可行的新技術,設計未曾有過的新型機械,主要包括功能設計和結構設計。
- 繼承設計:根據使用經驗和技術發展對已有的機械設計更新,以提高性能、降低製造成本或減少運行費用。
- 變型設計:為適應新的需要對已有的機械作部分的修改或增刪,從而發展出不同於標準型的變型產品。
機械設計是機械工程的重要組成部分,是決定機械性能的最主要因素。由於各產業對機械的性能要求不同而產生了許多專業性的機械設計,如紡織機械設計、礦山機械設計、農業機械設計、船舶設計、汽車設計、機床設計、壓縮機設計、內燃機設計、汽輪機設計和泵設計等。
機械設計的基本要求[3]
機械設計的基本要求是:在完成規定功能的前提下,性能好、效率高、成本低;在規定使用期間內安全可靠、操作方便、維護簡單和造型美觀等。一般應滿足以下幾方面要求。
(1)使用要求
使用要求是對機械產品的首要要求,是指機械產品必須滿足用戶對所需要的功能的要求,這是機械設計最根本的出發點。
(2)可靠性和安全性要求
機械產品在規定的使用條件下,在規定的時間內,應具有完成規定功能的能力。安全可靠是機械產品的必備條件。
(3)經濟性和社會性要求
經濟性要求是指所設計的機械產品在設計、製造方面周期短、成本低;在使用方面效率高、能耗少、生產率高、維護與管理的費用少等。此外,機械產品應操作方便、安全,具有宜人的外形和色彩,符合國家環境保護和勞動法規的要求。
(4)其他特殊要求
有些機械產品由於工作環境和要求不同,對設計提出了某些特殊要求。例如對航空飛行器有質量小、飛行阻力小和運載能力大的要求;流動使用的機械(如塔式起重機、鑽探機等)要便於安裝、拆卸和運輸;對機床有長期保持精度的要求;對食品、印刷、紡織、造紙機械等應有保持清潔,不得污染產品的要求等。
機械設計的原則[4]
談論機械設計應該遵循的原則時,以下六條是被普遍提到的,大家可以在以後的實際工作中慢慢體會。
(1)以市場需求為導向的原則
機械設計作為一種生產活動,與市場是緊密聯繫在一起的。從確定設計課題、使用要求、技術指標、設計與製造工期到拿出總體方案、進行可行性論證、綜合效用分析(著眼於實際使用效果的綜合分析)、盈虧分析直至具體設計、試製、鑒定、產品投放市場後的信息反饋等都是緊緊圍繞市場需求來運作的。設計人員要時時刻刻想著如何設計才能使產品具有競爭力,能夠占領市場,受到用戶青睞。
(2)創造性原則
創造是人類的本領。如果人類不能發揮自己的創造性,生產就不能得到發展,科技就不會進步,也就沒有人類的今天。設計只有作為一種創造性活動才具有強大的生命力。因循守舊,不敢創新,只能永遠落在別人後面。特別是在當今世界科技飛速發展的情況下,在機械設計中貫徹創造性原則尤為重要。
標準化、系列化、通用化簡稱為“三化”。“三化”是我國現行的一項很重要的技術政策,在機械設計中要認真貫徹執行。標準化是指將產品(特別是零部件)的質量、規格、性能、結構等方面的技術指標加以統一規定並作為標準來執行。我國的標準已經形成一個龐大的體系,主要有國家標準、行業標準等。為了與國際接軌,我國的某些標準正在迅速向國際標準靠攏。常見的標準代號有GB、JB等,分別代表中華人民共和國國家標準、機械工業標準。系列化是指對同一產品,在同一基本結構或基本條件下規定出若幹不同的尺寸系列。通用化是指在不同種類的產品或不同規格的同類產品中儘量採用同一結構和尺寸的零部件。
貫徹“三化”的好處主要是:減輕設計工作量,有利於提高設計質量並縮短生產周期;減少刀具和量具的規格,便於設計與製造,從而降低其成本;便於組織標準件的規模化、專門化生產;易於保證產品質量,節約材料,降低成本;提高互換性,便於維修;便於國家的巨集觀管理與調控以及內外貿易;便於評價產品質量,解決經濟糾紛。
(4)整體優化原則
設計要貫徹系統化和優化的思想。性能最好的機器其內部零件不一定是最好的;性能最好的機器也不一定是效益最好的機器。只要是有利於整體優化,機械部件也可以考慮用電子或其他元器件替代。總之,設計人員要將設計方案放在大系統中去考慮,尋求最優方案,應從經濟、技術、社會效益等各方面去分析、計算,權衡利弊,儘量使設計效果達到最佳。
(5)聯繫實際原則
所有的設計都不要脫離實際。設計人員特別要考慮當前的原材料供應情況,企業的生產條件,用戶的使用條件和要求等。
(6)人機工程原則
機器是為人服務的,但也是需要人去操作使用的。如何使機器適應人的操作要求;人機合一後,投入產出比率高,整體效果最好,這是擺在設計人員面前的一個課題。好的設計一定要符合人機工程學原理。
機械設計的一般方法[5]
在機械設計過程中,根據設計方案和機器的功能,一般將機器分為幾個主要部分,然後按照設計過程分別進行技術設計和結構設計,因此,技術設計和結構設計是針對主要零部件的設計,常用的設計和計算方法有以下幾種。
(1)理論設計。理論設計是一種創造性設計,也稱作開放性設計。設計者按機械零件的結構及其工作情況,將它簡化成一定的力學模型,運用理論力學、材料力學、彈性力學、塑性力學、流體力學、熱學、摩擦學理論等或利用這些理論推導出來的設計公式和實驗數據進行設計稱為理論設計。按照設計順序的不同,零件的理論設計計算可分為設計計算和校核計算。
設計計算是根據零件的工作情況、要求,進行失效分析,確定零件工作能力準則,並按其理論設計公式確定零件的形狀和尺寸;校核計算是先參照已有實物、圖紙和經驗數據,初步擬定出零件的結構和尺寸,然後根據工作能力準則所確定的理論校核公式進行校核計算。
(2)經驗設計。經驗設計也稱作繼承性設計,根據某些零件長期以來的設計與使用經驗歸納出經驗公式,或者設計者根據經驗用類比的方法,確定一些尺寸進行設計,稱為經驗設計。這對於某些典型零件是很有益的設計方法。例如減速箱體、傳動件、機床手柄等的某些結構尺寸。
(3)模型實驗設計。模型實驗設計也可以稱作實驗設計,對於一些尺寸大、結構複雜的重要零件,如大型水輪機、大型軋鋼機的關鍵零件,為了提高設計的可靠性,可以把初步設計的零部件或機器做成小模型或樣機,進行實驗,根據實驗結果改進產品的設計;而對於大量生產的機器(如汽車),則常用實物進行實驗。
在一部機器的設計中,有時會綜合使用以上三種設計方法,在設計不同部分時使用不同的方法。機器的設計是一項複雜的工程,通常要由一個設計集體合作完成。由於現代機器不僅是由機械部分組成,其他部分的設計與機械設計要配合,一般機械設計是為機器實現其功能提供硬體基礎,機器的控制、照明、冷卻等其他輔助部分通常在機械設計時都要統籌考慮,預留設計空間,切記機器是一個整體,機械設計是機器設計的一部分。
機械設計的一般過程[1]
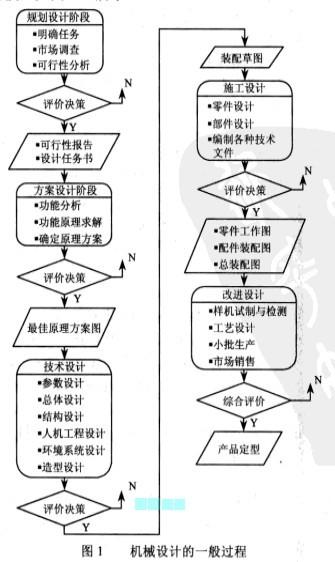
1.規劃設計
根據用戶訂貨需求、市場需要和新科研成果制訂設計任務。市場調查是在明確任務的基礎上廣泛地開展,內容主要包括用戶對產品功能、技術性能、價位、可維修性及外觀等的具體要求;國內外同類產品技術經濟情報;現有產品的銷售情況及對該產品的預測;原材料及配件供應情況;有關產品可持續發展的政策、法規等。可行性分析和報告是針對上述技術、經濟、社會等各方面信息進行詳細分析,並對開發的可能性進行綜合研究,提出產品開發的可行性報告,報告一般包括:
- 產品開發的必要性,市場需求預測。
- 有關產品的國內外水平和發展趨勢。
- 預期達到的最低目標和最高目標,包括設計技術水平、經濟和社會效益等。
- 在現有條件下開發的可能性論述及準備採取的措施。
- 提出設計、工藝等方面需要解決的關鍵問題。
- 投資費用預算及項目的進度、期限等。
技術任務書下達對開發產品的具體設計要求,它是產品設計、製造、試製等評價決策的依據,也是用戶評價產品優劣的尺度之一,內容主要包括:
- 產品功能、技術性能、規格及外形要求。
- 主要物理和力學參數、可靠性、壽命要求。
- 生產能力與效率的要求。
- 環境適應性與安全保護要求。
- 經濟性要求。
- 操縱、使用、維護要求。
- 設計進度要求。
2.方案設計
市場需求的滿足是以產品功能來體現的。實現產品功能是產品設計的核心,體現同一功能的原理方案可以是多種多樣的。因此,這一階段就是在功能分析的基礎上,通過創新構思、優化篩選,取得較理想的功能原理方案。產品功能原理方案的好壞,決定了產品的性能和成本,關係到產品的水平和競爭力,是這一設計階段的關鍵。
方案設計包括產品功能分析、功能原理求解、方案的綜合及評價決策,最後得到最佳功能原理方案。對於現代機械產品來說,其機械繫統(傳動系統和執行系統)的方案設計往往表現為機械運動示意圖(機械運動方案圖)和機械運動簡圖的設計。
3.技術設計
技術設計的任務是將功能原理方案得以具體化,成為機器及其零部件的合理結構。在此階段要完成產品的參數設計(初定參數、尺寸、材料、精度等)、總體設計(總體佈置圖、傳動系統圖、液壓系統圖、電氣系統圖等)、結構設計、人機工程設計、環境系統設計及造型設計等,最後得到總裝配草圖。
4.施工設計
施工設計的工作內容包括由總裝配草圖分拆零件圖,進行零部件設計,繪製零件工作圖、部件裝配圖;繪製總裝配圖;編製技術文件,如設計說明書、標準件及外購件明細表、備件和專用工具明細表等。
5.改進設計
改進設計包括樣機試製、測試、綜合評價及改進,以及工藝設計、小批生產、市場銷售及定型生產等環節。根據設計任務書的各項要求對樣機進行測試,發現產品在設計、製造、裝配及運行中的問題,細化分析問題。在此基礎上,對方案、整機、零部件做出綜合評價,對存在的問題和不足加以改進。
工藝設計包括以下兩方面的內容。
- 制定零件製造與裝配工藝,設計與生產批量相適應的工藝裝備及專用設備。
- 進行標準化、系列化檢查,儘量採用標準化、系列化、通用化的零部件,所有文檔資料符合標準化的要求。
通過小批生產及市場銷售反饋對產品設計、工藝設計及生產規模實踐考核,在進一步完善的基礎上,進入定型生產。
6.定型設計
定型設計用於成批或大量生產的機械。對於某些設計任務比較簡單(如簡單機械的新型設計、一般機械的繼承設計或變型設計等)的機械設計可省去初步設計程式。
必須強調指出,整個機械設計的過程是複雜的,並反覆進行。在某一階段發現問題,必須回到前面的有關階段進行並行設計。因此,整個機械設計是一個“設計—評估—再設計”不斷反覆、不斷修改、不斷優化完善的過程,以期逐漸接近最佳結果。
機械設計中的標準化[6]
在機械設計中,標準化的作用非常重要。標準化在簡化設計工作、縮短設計周期、提高設計質量、便於專業化生產、擴大互換性、便於維修、保證產品質量和降低成本等方面具有重要意義。
標準化包括三方面的內容,即零件標準化、產品系列化和部件通用化。
零件的標準化是對機械零件的種類、尺寸、結構要素、材料性能、檢驗方法、設計方法、公差配合及製圖規範等制定出相應的標準,供設計、製造及修配中共同遵照使用。如螺栓、螺母、墊圈等的標準化。
產品系列化是產品在同一基本結構或基本尺寸的條件下,按一定的規律優化組合成若幹個不同規格尺寸的產品。這樣可用較少規格的產品滿足不同的需要,如圓柱齒輪減速器系列。系列化是標準化的重要組成部分。
部件通用化是對不同規格的同類產品或不同類產品,在設計中儘量採用相同的零件或部件,如幾種類型不同的轎車可以採用相同的輪胎。通用化是廣義的標準化。
我國現行標準分為國家標準(GB)、行業標準(如JB、YB等)及企業標準三個等級。標準又分為必須執行的(如製圖標準、螺紋標準等)和推薦使用的(如直徑標準等)兩種。為了便於國際間的交流與合作,我國的國家標準現已儘可能地靠攏、符合和採用國際標準(ISO)。出口產品一般應符合國際標準(ISO)。
機械設計中的材料選用[3]
機械設計中常用的材料有鋼、鑄鐵、有色金屬(如鋁合金、銅合金等)和非金屬材料(如尼龍、工程塑料、橡膠等)。下麵介紹常用材料的選用原則。
1.滿足使用要求
滿足使用要求是選用材料的最基本原則和出發點。所謂使用要求,是指用所選材料做成的零件,在給定的工況條件下和預定的壽命期限內能正常工作。而不同的機械,其側重點又有差別。例如,當零件受載荷大並要求質量輕、尺寸小時,可選強度較高的材料;滑動摩擦下工作的零件,應選用減摩性能好的材料;高溫下工作的零件,應選用耐熱材料;當承受靜應力時,可選用塑性或脆性材料;而承受衝擊載荷時,必須選用衝擊韌度較好的材料等。
2.符合工藝要求
所謂工藝要求,是指所選材料的冷、熱加工性能好,熱處理工藝性好。例如,結構複雜而大批量生產的零件宜用鑄件,單件生產宜用鍛件或焊件。簡單盤狀零件(如齒輪或帶輪等),其毛坯是採用鑄件、鍛件還是焊件,主要取決於它們的尺寸大小、結構複雜程度及批量的大小;單件小批生產,宜用焊件;尺寸小、批量大、結構簡單,宜用模鍛件;結構複雜、大批量生產,則宜用鑄件。
3.綜合經濟效益要求
綜合經濟效益好是一切產品追求的最終目標,故在選擇零件材料時,應儘可能選擇能滿足上述兩項要求而價格低廉的材料。不能只考慮材料的價格,還應考慮加工成本及維修費用,即考慮綜合經濟效益。
- ↑ 1.0 1.1 1.2 應華,熊曉萍,張俊華等編著.第1章 基於Unigraphics軟體的機械設計基礎 UG NX 7.0機械設計行業應用實踐.機械工業出版社,2011.05.
- ↑ 王麗莉主編.第四章 機械設計及現代設計方法 機械工程概論.機械工業出版社,2011.02.
- ↑ 3.0 3.1 魏兵,楊文堤主編.緒論 機械設計基礎.華中科技大學出版社,2011.07.
- ↑ 林宋,夏新念,郭畢佳等編著.第十章 機械設計的綜合實例 機械設計師職場必備.機械工業出版社,2011.07.
- ↑ 張磊,王冠五主編.第一章 機械設計概述 機械設計.冶金工業出版社,2011.04.
- ↑ 林宋,夏新念,郭畢佳等編著.第四章 機械設計基礎知識 機械設計師職場必備.機械工業出版社,2011.07.