生產能力
出自 MBA智库百科(https://wiki.mbalib.com/)
生產能力(Production Capacity)
目錄[隱藏] |
生產能力是指在計劃期內,企業參與生產的全部固定資產,在既定的組織技術條件下,所能生產的產品數量,或者能夠處理的原材料數量。生產能力是反映企業所擁有的加工能力的一個技術參數,它也可以反映企業的生產規模。每位企業主管之所以十分關心生產能力,是因為他隨時需要知道企業的生產能力能否與市場需求相適應。當需求旺盛時,他需要考慮如何增加生產能力,以滿足需求的增長;當需求不足時,他需要考慮如何縮小規模,避免能力過剩,儘可能減少損失。
實際運用中的生產能力有多種不同的表達方式,包括:製程設計產能、有效產能和利用的產能等。
製程設計產能是企業建廠時在基建任務書和技術文件中所規定的生產能力,它是按照工廠設計文件規定的產品方案、技術工藝和設備,通過計算得到的最大年產量。 企業投產後往往要經過一段熟悉和掌握生產技術的過程,甚至改進某些設計不合理的地方,才能達到製程設計產能。製程設計產能也不是不可突破的,當操作人員熟悉了生產工藝,掌握了內在規律以後,通過適當的改造是可以使實際生產能力大大超過製程設計產能的。
企業在年度計劃中規定本年度要達到的實際生產能力稱為計劃能力。
計劃能力包括兩大部分。首先是企業已有的生產能力,是近期內的查定能力;其次是企業在本年度內新形成的能力。後者可以是以前的基建或技改項目在本年度形成的能力,也可以是企業通過管理手段而增加的能力。
計劃能力的大小基本上決定了企業的當期生產規模,生產計劃量應該與計劃能力相匹配。企業在編製計劃時要考慮市場需求量,能力與需求不大可能完全一致,利用生產能力的不確定性,在一定範圍內可以對生產能力作短期調整,以滿足市場需求。
對於老企業可能由於產品方向有所改變,或者是產品結構重新設計,也可能因為工藝方法有所改進等種種原因,當初的設計能力已完全不能反映實際情況,這時需要對企業的產能作重新核准,稱此結果為查定能力。 查定能力是企業的實際能力,對於企業各類計劃有指導作用,是企業計劃工作的基本參數。
在計算生產能力時,必須瞭解每條獨立生產線的情況、每家獨立工廠的生產水平以及整個生產系統的生產分配狀況,一般可通過以下步驟來進行:
1)運用預測技術預測每條獨立生產線的產品的銷售情況;
2)計算為滿足需求所需投入的設備和勞動力數量;
3)合理配置可獲得的設備與勞動力數量。
企業常常還要考慮一個生產能力餘量作為平衡設計生產能力與實際生產能力的緩衝。生產能力餘量是指超過預期需求的生產富餘能力。例如,某產品的預計需求為1000萬,而設計生產能力為1200萬。這樣,生產能力餘量為20%,即企業是以83%的生產能力利用率生產該產品。相反,如果一家企業的設計生產能力低於為滿足產品需求應達到的生產能力,則說明該企業的生產能力餘量為負值。比如一家企業的產品年需求量為1200萬,而其生產能力僅為1000萬,則該企業的生產能力餘量-20%。
生產能力的計量單位[1]
企業的生產能力是以企業生產的產品的數量來表示的。由於企業的生產類型不同,生產能力採用的計量單位也不同。對於大批大量生產類型企業,由於生產的品種比較單純而且穩定,一般用具體產品或代表產品來表示一個企業的生產能力,如某汽車製造廠的年生產能力是20萬輛紅旗小轎車,某化肥廠的年生產能力是30萬噸合成氨等。對於多品種、中小批量生產企業,由於生產的品種多,只能用代表產品或假設產品來表示企業的生產能力。
所謂代表產品,是指在企業生產的多種產品中具有典型性的、最能代表企業的專業方向的產品。作為代表產品必須在產品結構、生產工藝和勞動量構成上與其他產品相似且具有典型性。一般生產系列化產品的企業,常用代表產品來反映企業的生產能力,如電視機廠、電動機製造出等。例如,以B為代表產品,其換算方法見表1。
產品名稱 | 計劃產量 | 單位產品台時定額 | 摺合繫數 | 換算為代表產品 | 各產品所占比重/% | 按代表產品的生產能力 | 換算為各產品的生產能力(假設總能力為1000) |
---|---|---|---|---|---|---|---|
① | ② | ③ | ④ | ⑤ | ⑥=⑤/∑⑤ | ⑦ | ⑧=⑦×⑥/④ |
A | 300 | 50 | 0.5 | 150 | 150/920=16.30 | 假設企業的生產能力為1000台代表產品 | 1000×0.163/0.5=326 |
B | 500 | 100 | 1.0 | 500 | 500/920=54.35 | 1000×0.5435/1.0=543.5 | |
C | 150 | 120 | 1.2 | 180 | 180/920=19.57 | 1000×0.1957/1.2=163.08 | |
D | 50 | 180 | 1.8 | 90 | 90/920=9.78 | 1000×0.0978/1.8=54.33 | |
合計 | ∑⑤=920 | 100 |
當企業生產的產品品種較多,且產品結構和工藝過程各異時,應採用假定產品來表示企業的生產能力。假定產品是由企業生產的各種產品按其產量比重所構成的一種假想產品。假如企業生產A、B、C、D四種產品,各種產品的產量如表2所示,假定產品的勞動量可按表中所列的方法計算。
產品名稱 | 各產品的計劃產量 | 各產品產量占總產量的比重/% | 各產品某工種的單位產品台時定額 | 假定產品某工種的單位產品台時定額 |
---|---|---|---|---|
① | ② | ③=②/∑② | ④ | ⑤=④×③ |
A | 56 | 26.42 | 9.6 | 2.5363 |
B | 72 | 33.96 | 7.8 | 2.6489 |
C | 48 | 22.64 | 1.8 | 0.4075 |
D | 36 | 16.98 | 6.5 | 1.1037 |
合計 | ∑②=212 | ∑③=100.0 | ∑⑤=6.6964 |
按以上例子,相當於一臺假設產品中含0.2642台A產品,0.3396台B產品,0.2264台C產品,0.1698台D產品。這時假設產品某工種的單台定額,就是各產品的單台定額分別乘以各產品的產量比重的加權值,如表中所示的6.6964。
生產能力的計算[1]
一個企業的生產能力取決於其主要車間或多數車間的生產能力經綜合平衡後的結果。一個車間的生產能力取決於其主要生產工段(生產單元)或大多數生產工段(生產單元)的生產能力經綜合平衡後的結果。一個生產工段(生產單元)的生產能力,則取決於該工段內主要設備或大多數設備的生產能力經綜合平衡後的結果。所以計算企業的生產能力,應從企業基層生產環節的生產能力算起,即從生產車間內各設備組的生產能力算起。
設備組生產能力的計算公式如下:
式中:M——計劃期內某設備組的生產能力,台(產品)/年;
S——該設備組內設備的數量,台(設備);
Fe——該類設備計劃期內的單台有效工作時間,小時/年、台;
t——單位產品該工種的台時定額,小時/台(產品)。
一條生產線的生產能力計算公式如下:
M——計劃期內該生產線的生產能力,台(產品)/年;
Fe——計劃期內該生產線的有效工作班數,班/年。
【例1】某機械製造廠生產小型電動機H、G、R、S等型號系列,今選R為其代表產品,如已知機械加工車間的主軸生產單元有數控車床7台,每臺車床的制度工作班數為42班/月,其中有一臺車床在計劃期內適逢中修,要占用3個工作班。R型代表產品的單臺車工工時定額為6個台時。該主軸生產單元數控車床組的生產能力可計算如下:
(台/月)
由上可知計劃月內主軸生產單元數控車床組的生產能力為388台代表產品(R)。
【例2】某廠機械加工車間銑工工段有5台萬能銑床,制度工作時間為每台機床每月42個工作班,每班8小時。若有效工作時間是制度工作時間的95%,車間生產A、B、C、D四種產品結構和工藝過程均不相同的產品。A、B、C、D四種產品的產量和工時定額如採用表2中的數據,則假定產品銑工工序的單台定額為6.6964小時。由此可以算出計劃月內銑工工段的生產能力為:
(台/月)
根據上式計算,該銑工工段的生產能力為238.35台假定產品。如把以假定產品表示的生產能力轉換為各具體產品的生產能力,則可計算如下:
生產A產品的能力:(台);
生產B產品的能力:(台);
生產C產品的能力:(台);
生產D產品的能力:(台)。
對於多品種小批量生產的企業,由於生產的品種變化大,在計算計劃期的生產能力時,用代表產品和假定產品作計量單位都不方便或不合適。通常直接採用“台時”計算,即計算該設備組在計劃期內可以提供的工作時間。在進行生產能力平衡時,將計算所得的台時數與計劃期安排在該設備組上加工的各產品的加工工作量進行對照比較,以檢驗該設備組的生產能力能否滿足計劃期生產任務的要求。
一個單位各設備組的實際生產能力是不會完全相等的,如圖1所示:
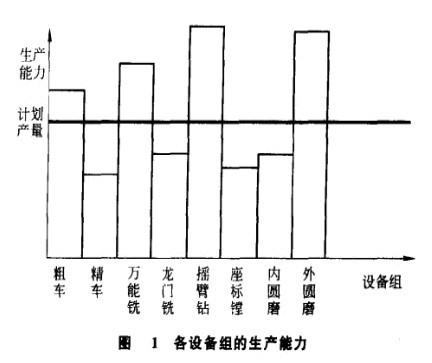
各設備組的生產能力有的高,有的低,與計劃要求的能力有一定出人。如不採取措施則該單位的生產能力水平,將取決於諸設備組中生產能力最低的環節。此時應進行生產能力的綜合平衡,就是要採取措施設法提高薄弱環節的生產能力,使之接近大多數設備組的生產能力,使該單位的實際生產能力達到合理的水平。
當企業不能適應市場的變化,因經營不佳而陷入困境時,需要進行產能收縮。在收縮中應儘可能減少損失,力爭在收縮中求得新的發展。下麵介紹產能收縮的幾條途徑:
1.逐步退出無前景行業
經過周密的市場分析,如果確認本企業所從事的行業行將衰退,企業就需要考慮如何退出該行業。由於市場衰退是預測分析的結果,還不是現實,企業只不過在近年中感覺到衰退的跡象。所以企業首先停止在此行業的投資,然後分階段地撤出資金和人員。之所以採取逐步退出的策略,是因為還有市場。另外,企業資金的轉移也不是一件很容易的事情,企業不能輕易放棄還有利可圖的市場,這樣做可以儘可能地減少損失。
2.出售部分虧損部門
對於一些大企業,如果某些子公司或分廠的經營狀況很差,消耗企業大量的資源,使公司背上了沉重的負擔,扭虧又無望,這時不如拋售虧損部門。這個方法是西方企業處理虧損子公司所通常採用的方法。對待出售資產的決策應有積極的態度,出售是收縮,但收縮是為了卸掉包袱,爭取主動,為發展創造條件。
3.轉產
如果本行業已日暮途窮,而企業的設備還是比較先進的,員工的素質也很好,可以考慮轉向相關行業。由於是相關行業,加工工藝相似,大部分設備可以繼續使用,員工們的經驗可以得到充分的發揮。例如,服裝廠可以轉向床上用品和居室裝飾品,食品廠可以轉向生產動物食品等等。
在生產過程中,企業有時可能需要擴大產能。企業在擴大其生產能力時,應考慮許多方面的問題,其中最重要的幾個方面是維持生產系統的平衡,控制擴大生產能力的頻率以及有效利用外部生產能力。
1.維持生產系統的平衡
在一家生產完全平衡的工廠里,生產第一階段的輸出恰好完全滿足生產第二階段輸入的要求,生產第二階段的輸出又恰好完全滿足生產第三階段的輸入要求,依次類推。然而,實際生產中達到這樣一個“完美”的設計幾乎是不可能的,而且也是人們不希望的,因為其一:每一生產階段的最佳生產水平不同,其二:產品需求是會發生變化的,而且由於生產過程本身的一些問題也會導致生產不平衡的現象發生,除非生產完全是在自動化生產線上進行,因為一條自動化生產線就像是一臺大機器一樣,是一個整體。
解決生產系統不平衡問題的方法有很多。例如:一,增大瓶頸的生產能力。可採取一些臨時措施,如加班工作、租賃設備、通過轉包合同購買其他廠家的產成品等;二,在生產瓶頸之前留些緩衝庫存,以保證瓶頸環節持續運轉,不會停工;三,如果某一部門的生產依賴於前一部門的生產,那麼就重覆設置前一部門的生產設備,可以充足地生產以便供應下一部門的生產所需。
2.擴大生產能力的頻率
在擴大生產能力時,應考慮兩種類型的成本問題:生產能力升級過於頻繁造成的成本與生產能力升級過於滯緩造成的成本。首先,生產能力升級過於頻繁會帶來許多直接成本的投入,如舊設備的拆卸與更換、培訓工人、使用新設備等等。此外,升級時必須購買新設備,新設備的購置費用往往遠大於處理舊設備回收的資金量。最後,在設備更換期間,生產場地或服務場所的閑置也會造成機會成本。
反之,生產能力升級過於滯緩也會有很大的成本支出。由於生產能力升級的間隔期較長,每次升級時,都需要投入大筆資金,大幅度地擴大生產能力。然而,如果當前尚不需要的那些生產能力被閑置,那麼,在這些閑置生產能力上的投資就將作為管理費用計入成本,這就造成了資金的占用和投資的浪費。
3.外部生產能力
有些情況下還可以利用一種更為經濟有效的辦法,那就是不擴大本企業的生產能力,而是利用現有的外部生產能力來增加產量。常用的兩種方式分別是:簽訂轉包合同或共用生產能力。共用生產能力的新途徑還有利用一種企業聯合體間的分時柔性工廠等。
可由企業對生產能力加以調節控制的因素很多。從計劃的觀點看,可將這些因素按取得能力的時間長短,分為長期、中期和短期三類。
1、長期因素
取得生產能力的時間在一年以上的都可歸入長期因素。它們包括:建設新廠、擴建舊廠、購置安裝大型成套設備、進行技術改造等。這些措施都能從根本上改變生產系統的狀況,大幅度地提高生產能力,但同時也需要大量的資金投入。應用這些因素屬於戰略性決策。
2、中期因素
在半年到一年之內對生產能力發生影響的那些因素為中期因素。如採用新的工藝裝備、添置一些可隨時買到的通用設備,或對設備進行小規模的改造或革新;增加工人,以及將某些生產任務委托其他工廠生產等,其中,也包括利用庫存來調節生產的作用。這些因素是在現有生產設施的基礎上所作的局部擴充。它們屬於中層管理的決策。一般在年度生產計劃的制定與實施中加以考慮。
3、短期因素
在半年之內以至當月就能對生產能力產生影響的屬於短期因素。這類因素很多,如:
1)加班加點;
2)臨時增加工人,增開班次;
3)採取措施降低廢品率;
4)改善原材料質量;
5)改善設備維修制度。這能減少設備故障時間,提高設備利用率而提高生產能力;
6)採用適當的工資獎勵制度,激發工人的勞動積極性,在短時間內提高生產;
7)合理選擇批量。批量選擇的不同會影響設備調整時間的變化。合理選擇批量能減少不必要的設備調整時間,而提高設備利用率,即提高了設備的生產能力;
生產能力的短期調節因素是對現有生產設施利用的改善,都屬於作業層的決策。
本条目由以下用户参与贡献
村姑,苦行者,funwmy,Angle Roh,Kuxiaoxue,Zfj3000,Cabbage,Vulture,Dan,KAER,HEHE林,方小莉,Yixi,Gaoshan2013,连晓雾,寒曦,刘维燎.評論(共4條)
沒有實際的計算例子,只有空的理論,不好用。比如說:同一條流水線可以生產3種產品,我在計算每種產品的生產能力時是該流水線只生產該種產品,不生產其它產品的產量,還是要均衡考慮三種產品在流水線上的年產量分配。
沒有實際的計算例子,只有空的理論,不好用。比如說:同一條流水線可以生產3種產品,我在計算每種產品的生產能力時是該流水線只生產該種產品,不生產其它產品的產量,還是要均衡考慮三種產品在流水線上的年產量分配。
已更新添加原文計算部分的內容,希望對您有幫助!~
有些片面,更多的按傳統觀念強調的是設備廠房等物的產能, 人為的管理因素對產能影響沒有考慮,有用不先進。