組合機床
出自 MBA智库百科(https://wiki.mbalib.com/)
組合機床(Aggregate Machine Tool)
目錄[隱藏] |
什麼是組合機床[1]
組合機床是由大量的通用部件和少量的專用部件組成的工序集中的高效率專用機床。它能夠對一種(或幾種)零件進行多刀、多軸、多面、多工位加工。在組合機床上可以完成鑽孔、擴孔、鉸孔、鏜孔、攻絲、車削、銑削、磨削及滾壓等工序,生產效率高,加工精度穩定。
組合機床的特點[1]
(1)組合機床上的通用部件和標準零件約占全部機床零、部件總量的70%~80%,因此設計和製造的周期短,投資少,經濟效益好。
(2)由於組合機床採用多刀加工,並且自動化程度高,因而比通用機床生產效率高,產品質量穩定,勞動強度低。
(3)組合機床的通用部件是經過周密設計和長期生產實踐檢驗的,又有專門廠成批製造,因此結構穩定、工作可靠,使用和維修方便。
(4)在組合機床上加工零件時,由於採用專用夾具、刀具和導向裝置等,加工質量靠工藝裝備保證,對操作工人的技術水平要求不高。
(5)當被加工產品更新時,採用其他類型的專用機床時,其大部分部件要報廢。用組合機床時,其通用部件和標準零件可以重覆利用,不必另行設計和製造。
(6)組合機床易於連成組合機床自動線,以適應大規模的生產需要。
組合機床通用部件的分類[1]
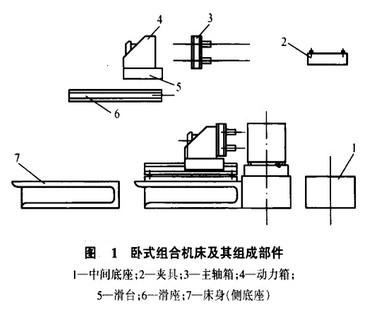

(1)動力部件
動力部件是傳遞動力實現進給運動或主運動的部件,是通用部件中的主要部件,其他部件是以動力部件為基礎來配套選用的。動力部件的結構和性能基本上決定了組合機床的使用性能。
在我國組合機床通用部件的新標準中,已經取消了機械動力頭和液壓動力頭,而是以動力滑台為基礎組成的動力部件。動力部件包括液壓滑台、機械滑台、動力箱、銑削頭、鏜削頭、鑽頭、液壓鏜孔車端面頭等等。由滑台實現進給運動,在滑臺上再安裝一個實現刀具主運動的通用動力箱。動力箱前端安裝一個專用的多軸箱,用來完成鑽、擴、鉸、鏜、鍃窩、倒角、攻絲等工序。動力滑臺上還可以安裝銑削頭、鏜削頭、鏜孔車端面頭等。
(2)支承部件
支承部件是組合機床的基礎部件,用於支承和連接機床所有部件,由它們組成一定的組合機床,並使這些部件在工作時保持準確的相對位置。
支承部件包括側底座(側底座上面安裝的是作水平方向進給運動的動力部件)、立柱(安裝在立柱上的動力部件是作豎直方向進給運動的)、立柱底座、中間底座(在它上面安裝夾具部件)等。側底座、立柱底座和中間底座之間用鍵定位,但也允許用錐銷定位。
(3)輸送部件
輸送部件用於完成夾具和工件的移位或轉位,包括迴轉工作台和移動工作台等。在多工位組合機床上必須應用這種輸送部件。輸送部件的分度和定位精度直接影響多工位組合機床
輸送部件用於完成夾具和工件的移位或轉位,包括迴轉工作台和移動工作台等。在多工位組合機床上必須應用這種輸送部件。輸送部件的分度和定位精度直接影響多工位組合機床的加工精度。
(4)控制部件
控制部件用於控制組合機床,使組合機床按預定的程式完成工作迴圈。控制部件包括各種液壓元件、操縱板、控制擋鐵及按鈕等。
(5)輔助部件
輔助部件包括用於自動夾緊工件的氣動裝置、液壓裝置、機械扳手,以及冷卻、潤滑、排屑等裝置。
組合機床的通用部件按其功率大小分為大型和小型兩大類。大型通用部件是指電動機功率為1.5~30 kW的動力部件及配套部件。小型通用部件是指電動機功率為0.1~2.2 kW的動力部件及配套部件。
組合機床的通用部件,絕大多數已有國家標準,並按標準所規定的名義尺寸、主參數、互換尺寸等定型,各種通用部件之間有配套關係。這樣,用戶可根據被加工零件的尺寸、形狀和技術要求等,選用通用部件,組成不同形式的組合機床,以滿足生產的需要。
組合機床的配置及工藝範圍[1]
組合機床的形式很多,根據工件的不同加工要求,採用各種結構的通用部件,就可以靈活地組成各種不同配置(佈局)形式的組合機床。按照配置形式,組合機床可分為單工位組合機床和多工位組合機床兩大類。
單工位組合機床的特點是,工件只能在一個工位上進行加工,通常是用於加工一個或兩個工件,特別適用於大、中型箱體件的加工。根據被加工工件的錶面情況,單工位組合機床又有單面加工、雙面加工、三面加工和四面加工等幾種。
卧式配置的組合機床,動力部件是沿水平方向運動的,這種組合機床多用於加工孔中心線與定位基準面平行而又需要由一面或幾面同時加工的箱體件。動力部件沿豎直方向上下運動的配置形式,稱為立式組合機床。立式組合機床適合加工定位基準面是水平的,而加工的孔與基準面相垂直的工件。同時配置有沿水平方向和豎直方向運動動力部件的機床,稱為複合式配置的組合機床。傾斜配置形式的組合機床主要用於加工傾斜錶面。
多工位組合機床的特點是,工件能在幾個工位上進行加工。需要多部位加工的中、小零件常用一臺多工位組合機床完成工件的全部工序。由於多工位機床的工序集中程度和生產效率高,所以常常用於大批、大量生產中。在多工位組合機床上工件工位的變換,有用人工換裝和機動變位兩種方式。
組合機床已經在汽車、柴油機、電機、儀錶、航空、冶金等行業得到了廣泛的使用,組合機床最適宜於大批、大量生產部門,但在一些中、小批生產部門也已開始推廣使用。組合機床最適合於加工殼體類零件,如氣缸體、氣缸蓋、變速箱體、機座等。這些零件從平面到孔的全部加工工序都可以由組合機床來完成。
組合機床可完成的工藝有銑平面、刮平面、車端面、鑽孔、擴孔、鏜孔、鉸孔、攻絲、倒角、鍃窩、鑽深孔、切槽等。隨著綜合自動技術的發展,組合機床可完成的工藝範圍也在不斷擴大,除了上述工藝外,還可完成車外圓、車錐面、車弧面、切削內外螺紋、滾壓孔、拉削內外圓柱面和平面、磨削、拋光、珩磨,甚至還可以進行衝壓、焊接、熱處理、裝配、自動測量和檢查等。
組合機床的設計[2]
一、組合機床的設計特點
由於組合機床是由大量通用零、部件和少量專用零、部第一節組合機床設計步驟一、組合機床的設計特點由於組合機床是由大量通用零、部件和少量專用零、部件組成的專用機床,因此,它的設計具有如下特點:
1)組合機床設計時必須首先確定加工產品的生產類型,以便根據不同的生產類型選擇合理的組合機床的配置形式。因為在製造組合機床過程中,有些通用零、部件要經過補充加工,專用件、夾具及刀具隨產品而有所不同。變更產品的加工要求或尺寸以及變更產品本身,常常會使整台組合機床要重新調整,或必須進行重新的設計和製造。
2)組合機床的設計與產品的加工工藝有非常密切的聯繫,因此,在設計組合機床前,一定要做好調查研究,在總結經驗的基礎上來決定被加工產品的工藝過程、加工方法、定位夾緊方法等。因為組合機床設計的先進性與可靠性,除了與機床本身的結構有關外,在很大程度上決定於工藝方案的先進性與可靠性。
3)在選擇通用部件和進行專用件的設計時,應堅持盡最大可能採用通用件的原則,這對於加快組合機床設計和製造速度有決定性的意義。當通用件不能滿足機床工作要求時,才設計專用件。而這種專用件也應該考慮儘可能與通用件接近(結構、形式、尺寸等),以便簡化設計和製造工作,提高零件的通用化程度。
4)組合機床的加工精度在相當大的程度上是依靠組合機床零、部件的安裝調整精度來保證的,因此,在設計時,應考慮裝配調整的可靠與方便。
5)對於自動線上用的組合機床,應該把組合機床自動線看成一個有機的整體,從設計一開始就考慮自動線的總體、自動運輸裝置及其與機床夾具之間的聯繫以及自動線上其他輔助裝置的安排等問題。在整個設計過程中,機床設計和自動線運輸裝置和其他輔助裝置的設計可以平行交叉進行,但機床和夾具設計需服從自動線總體設計的需要。
二、組合機床的設計步驟
1.調查在明確設計任務之後,應該進行下列工作:
1)瞭解被加工零件在機器中的作用,工件的加工部位、技術要求、裝配關係及其生產綱領。
2)深入現場。詳細瞭解相同類型的產品和生產規模,基本相近的被加工零件的整個工藝過程。其中包括機床、夾具、刀具和其他附屬結構和性能;工件的定位基面和夾壓點;切削用量、加工餘量及刀具壽命所能達到的精度和光潔度;毛坯分型面、飛邊等情況;產生廢品的原因;自動化的可靠程度;電氣、液壓設備的工作情況;自動線的運輸裝置和其他輔助設備的結構工作情況等,並聽取操作工人的經驗和改進意見。
3)瞭解生產廠的製造能力及技術水平。
4)瞭解使用廠的技術水平,如:能否製造和修理液壓設備,有無壓縮空氣站,工夾具的製造和維修能力及能否製造複雜刀具等。
5)收集有關資料,並加以分析比較。
6)確定採用新工藝的方法,對一些需要保證技術條件而沒有經過生產實際考驗的工藝方法進行必要的試驗。
2.製造工藝方案
1)對工件進行工藝分析,並根據毛坯情況結合組合機床的工藝可能性和可能達到的精度,初步確定工件的工藝過程。
2)選擇定位基準,決定定位、夾緊方式。
3)詳細擬定被加工零件的工藝路線,即決定各錶面的加工方法及順序,決定工序(包括熱處理、檢驗工序及其他)、工位(包括裝卸工位)和工步,初步確定組合機床的配置形式及其總體佈局。
4)確定加工餘量和工序尺寸,併進行必要的尺寸鏈換算。
5)繪製被加工零件的工序圖。
6)決定刀具種類、形式、尺寸、安裝方法及輔助工具(接桿、卡頭等)的尺寸,併進行切削用量的選擇。
7)決定夾具的定位、導向、夾緊機構的方案及外形尺寸。
8)繪製加工示意圖,決定機床的工作迴圈。
9)電腦床的生產率和負荷率,編製機床的生產率計算卡。
10)審查及通過工藝方案。
3.機床總體設計
1)計算切削力、進給力、動力部件的最大功率。
2)選擇動力部件的類型、型號、規格和配套部件。
3)選擇機床的支承及零件輸送部件(滑座、側底座、立柱、立柱底座及工作台等),並決定中間底座的主要尺寸,冷卻、排屑系統等。
4)繪製機床聯繫尺寸圖。
5)擬定液壓、電氣控制系統方案。
6)審查及通過機床的設計方案。
4.部件設計
根據機床的聯繫尺寸圖及工藝要求設計組合機床的各部件。在設計過程中如果發現擬定的方案有不合理的地方,應當進行及時的修改。部件設計的內容包括:
1)夾具設計。
2)多軸箱設計。
3)專用刀具設計。
4)液壓系統設計。
5)電氣系統設計。
6)其他部件設計:如中間底座、潤滑冷卻系統等。
5.工作圖設計
1)繪製通用零件的補充加工圖、專用零件圖等。
2)繪製各部件總圖、潤滑冷卻管路圖、液壓管路圖、氣動管路圖、電氣控制線路圖、電氣線路安裝圖等。
3)修改和最後確定機床聯繫尺寸圖、工序圖、加工示意圖、生產率計算卡。
4)繪製機床總酎。
5)編製機床所需要的各種明鈿表,如:零件明細表、標準件明細表、外購件明細表等。
6)編製機床使用說明書,包括機床驗收精度要求、潤滑卡、地基圖等。
一、組合機床最常用的加工範圍
1.孔加工
對於一般尺寸較小的孔,可以用鑽、擴、鉸等刀具分幾次加工,或採用複合刀具加工,還可以用普通刀具或複合刀具進行端面、沉孔、埋頭孔、倒角等。
對於尺寸較大孔,可以用粗鏜、半精鏜、高速精鏜的方法進行加工,可以用剛性主軸或有導向裝置的浮動鏜桿進行加工。加工時可以採用單刀,也可以採用多刀進行加工;此外還可以加工孔的端面、倒角及挖槽等。
對於大的錐孔,可以採用特種工具進行加工。
在組合機床上還可以實現一些其他的孔的精加工工序,如擠壓孔、滾壓孔等。對於加工深度精度要求不高的止口,可以採用死擋鐵來控制止口深度。但對於加工深度要求較高的止口,則必須採用特種工具進行加工。
2.螺紋加工
一般緊固螺紋孔可以在鑽孔、倒角後攻絲動力頭或攻絲主軸。
對於外螺紋可以用自動板牙頭來切削。
3.平面及直槽加工
平面和直槽一般採用銑削動力頭進行加工。可以是銑頭移動,也可以是工件移動。對於加工與孔垂直的大端面,可以採用鏜孔車端面動力頭進行加工;若是小端面,則可採用鍃端面的方法進行加工。
4.其他
利用組合機床的動作可以進行不太長外圓的套車、自動測量等。
二、組合機床加工所能達到的精度和錶面粗糙度
1.孔本身的精度和錶面粗糙度
1)對於在鑄鐵及銅件上加工IT8級精度的孔時,一般需經過3次加工,錶面粗糙度可達到Ra5;若加工IT6級精度的孔時,則需要3~4次加工,錶面粗糙度可達到Ra2.5以上;當採用精鏜或滾壓加工時,精度可達到IT6級,錶面粗糙度可達Ra1.25以上。
2)對於在鑄鐵件上加工IT8級精度的孔時,一般需要2次加工,錶面粗糙度可達Ra2.5;加工IT7級精度的孔時,需經過2~3次加工,錶面粗糙度可達Ra1.25;加工IT6級精度的孔時,需經過3~4次加工,錶面粗糙度可達Rai.25;對於加工IT6~IT5級精度的孔時,則需要經過4~5次加工,錶面粗糙度為Ral.25。
3)加工有色金屬件時,若經過3~4次加工,可以穩定地達到IT6~IT5級精度,錶面粗糙度可達Ra0.63~0.16。
上述三種材料在組合機床及自動線上進行加工時,一般對於IT6級、IT5級精度孔的橢圓度,可以控制到接近孔的公差;對於IT6級精度以下孔的橢圓度及圓柱度,可控制在孔的加工公差範圍的一半以內。
4)對於加工螺紋孔,精度一般可以達到IT7級;當採用特殊結構的工具進行加工時,可以達到IT6級精度。
2.孔的同軸度
1)若由一面鏜孔,鏜桿採用後或多層精密導向,孔的同軸度可以控制在0.015~0.03mm範圍內。
2)若採用單軸兩面鏜孔,使用調整主軸位置精度時,孔的同軸度也可達0.015~0.03mm。
3)若多軸從兩面加工,孔的同軸度一般為0.05mm。
3.孔的平行度
鏜孔軸線之間的平行度以及孔對定位基面的平行度,一般可保持在軸線間距離公差的範圍以內。在調整精度時,也可以達到(O.02~0.05)/(800~1000)。
4.孔的位置精度
孔的位置精度是指孔與孔之間,或孔與定位基面之間的位置尺寸精度。
在鏜孔時,採用固定精密導向,孔的位置精度可以達到±0.025~±0.05mm,採用其他加工方法可以達到±0.05mm。
對於多工位迴轉工作台機床和鼓輪式機床,在一個工位上精加工出來的孔的位置精度也可以達到±0.05mm;但是在兩個工位上分別精加工出來的孔,位置精度就較低,對於立式多工位迴轉工作台機床可達到±0.1mm,鼓輪式機床只能達到±0.2mm左右。鑽孑L的位置精度,若採用固定導向一般可以達到±0.2mm;若減小導向套與鑽頭之間的間隙,且導向套距工件較近時,則可以達到±0.15mm;若用活動模板鑽孔,且活動板用定位銷與夾具定位時,則其位置精度一般可達±0.2~±0.25mm。螺紋孔位置精度主要決定於鑽孔的位置精度,一般可以達到±0.25mm;當鑽孔的位置精度較好時,可以達到±0.15mm。
5.孔的垂直度
被加工孔的軸心線對基面或對另一被加工孔的軸心的垂直度,均可達到0.02/1000
6.止口深度
多軸加工採用動力頭在死擋鐵上停留的方法,止口深度精度能達到0.15~0.25mm;單軸進給,若採用特殊結構的工具,加工到終點時用擋鐵塊頂在工件的錶面上,一般可達到0.08—0.10mm;當採用工具的加工精度較高時,可以保證在0.02.0.045mm以內。
7.平面加工精度
加工平面的平面度可以達到0.05mm,錶面粗糙度可以達到Ra2.5,被加工平面對基面的平行可以控制在0.05mm以內,被加工平面到基面的距離尺寸公差亦可以保證在0.05mm以內。
組合機床的發展趨勢[1]
1.提高通用部件的水平
通用部件技術水平的主要標準是:品種規格齊全,動、靜態性能參數先進,工藝性好j精度高和精度保持性好。目前應註意開發適應強力銑削的大功率動力滑台、高精度鏜削頭和高精度滑台,以及適應中、小批生產的快調、速換動力部件和支承部件。
2.發展適應中、小批生產的組合機床
在機械製造工業中,中、小批生產約占80%。在某些中批生產的企業中,如機床、閥門行業等,其關鍵工序採用組合機床。其中機床廠用組合機床加工主軸變速箱孔系,產品質量穩定,生產效率高,技術經濟效果顯著。發展具有可調、快調、裝配靈活、適應多品種加工特點的組合機床十分迫切。轉塔主軸箱式組合機床、可換主軸箱式組合機床以及自動換刀式數控組合機床可用於中、小批生產,但這類機床結構複雜,成本較高。
3.採用新刀具
近年來出現了多種新刀具,如具有鍍層的硬質合金刀片、立方氮化硼刀具、金剛石刀具、各種可轉位的密齒銑刀、噴吸鑽頭、鑲有可轉位刀片的“短鑽頭”等。一般情況下,採用先進刀具的工時為原工時的1/4~1/2。因為提高了刀具的耐用度,所以大大縮短了多刀組合機床停機換刀時間,提高了組合機床的經濟效益。
4.發展自動檢測技術
自動檢測包括對毛坯尺寸和工件硬度的檢查、鑽孔深度、刀具折斷、精加工尺寸和幾何形狀的檢查等。檢查方法分為主動檢查與被動檢查。主動檢查是將不合格的工件剔出,使之不往下個工位輸送。被動檢查則是發現不合格的工件時發出停機信號。目前主動檢查應用得日趨廣泛。隨著電子元件的迅速發展,集成控制器、微處理機的應用,自動檢測技術顯得更加可靠。自動檢測工位要進行數據處理,統計計算以及列印出有關數據或作數字顯示。自動檢測技術的發展可以把被加工零件的實際尺寸控制在比規定公差更小的範圍之內。還可以把加工後的工件按公差帶進行分組,以便按分組的公差帶裝配。實際表明,採用分組裝配法提高產品的精度要比單純提高設備精度更為經濟。
5.擴大工藝範圍
組合機床除完成切削加工等工序外,還在逐步設計製造用於焊接、熱處理、自動裝配、自動列印、性能試驗以及清洗和包裝等用途的組合機床。