傳動裝置
出自 MBA智库百科(https://wiki.mbalib.com/)
目錄[隱藏] |
什麼是傳動裝置[1]
傳動裝置是指把動力源的運動和動力傳遞給執行機構的裝置,介於動力源和執行機構之間,可以改變運動速度,運動方式和力或轉矩的大小。
傳動裝置的分類[2]
任何一部完整的機器都由動力部分、傳動裝置和工作機構組成,能量從動力部分經過傳動裝置傳遞到工作機構。根據工作介質的不同,傳動裝置可分為四大類:機械傳動、電力傳動、氣體傳動和液體傳動。
(1)機械傳動
機械傳動是通過齒輪、皮帶、鏈條、鋼絲繩、軸和軸承等機械零件傳遞能量的。它具有傳動準確可靠、製造簡單、設計及工藝都比較成熟、受負荷及溫度變化的影響小等優點,但與其他傳動形式比較,有結構複雜笨重、遠距離操縱困難、安裝位置自由度小等缺點。
(2)電力傳動
電力傳動在有交流電源的場合得到了廣泛的應用,但交流電動機若實現無級調速需要有變頻調速設備,而直流電動機需要直流電源,其無級調速需要有可控硅調速設備,因而應用範圍受到限制。電力傳動在大功率及低速大轉矩的場合普及使用尚有一段距離。在工程機械的應用上,由於電源限制,結構笨重,無法進行頻繁的啟動、制動、換向等原因,很少單獨採用電力傳動。
(3)氣體傳動
氣體傳動是以壓縮空氣為工作介質的,通過調節供氣量,很容易實現無級調速,而且結構簡單、操作方便、高壓空氣流動過程中壓力損失少,同時空氣從大氣中取得,無供應困難,排氣及漏氣全部回到大氣中去,無污染環境的弊病,對環境的適應性強。氣體傳動的致命弱點是由於空氣的可壓縮性致使無法獲得穩定的運動,因此,一般只用於那些對運動均勻性無關緊要的地方,如氣錘、風鎬等。此外為了減少空氣的泄漏及安全原因,氣體傳動系統的工作壓力一般不超過0.7~0.8MPa,因而氣動元件結構尺寸大,不宜用於大功率傳動。在工程機械上氣動元件多用於操縱系統,如制動器、離合器的操縱等。
(4)液體傳動
以液體為工作介質,傳遞能量和進行控制的叫液體傳動,它包括液力傳動、液黏傳動和液壓傳動。
1)液力傳動
它實際上是一組離心泵一渦輪機系統,發動機帶動離心泵旋轉,離心泵從液槽吸入液體並帶動液體旋轉,最後將液體以一定的速度排入導管。這樣,離心泵便把發動機的機械能變成了液體的動能。從泵排出的高速液體經導管噴到渦輪機的葉片上,使渦輪轉動,從而變成渦輪軸的機械能。這種只利用液體動能的傳動叫液力傳動。現代液力傳動裝置可以看成是由上述離心泵一渦輪機組演化而來。
液力傳動多在工程機械中作為機械傳動的一個環節,組成液力機械傳動而被廣泛應用著,它具有自動無級變速的特點,無論機械遇到怎樣大的阻力都不會使發動機熄火,但由於液力機械傳動的效率比較低,一般不作為一個獨立完整的傳動系統被應用。
2)液黏傳動
它是以黏性液體為工作介質,依靠主、從動摩擦片間液體的黏性來傳遞動力並調節轉速與力矩的一種傳動方式。液黏傳動分為兩大類,一類是運行中油膜厚度不變的液黏傳動,如硅油風扇離合器;另一類是運行中油膜厚度可變的液黏傳動,如液黏調速離合器、液黏制動器、液黏測功器、液黏聯軸器、液黏調速裝置等。
3)液壓傳動
它是利用密閉工作容積內液體壓力能的傳動。液壓千斤頂就是一個簡單的液壓傳動的實例。液壓千斤頂的結構如圖1(a)所示,為明瞭起見,用符號表示其有關零部件,畫出它的液壓系統,如圖1(b)所示。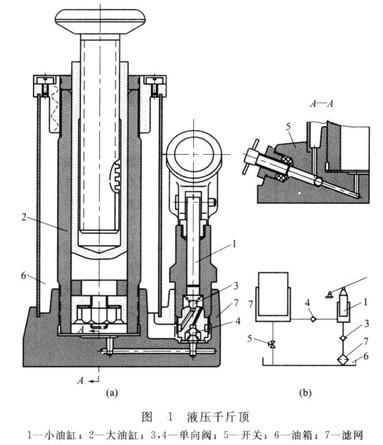
液壓千斤頂的小油缸l、大油缸2、油箱6以及它們之間的連接通道構成一個密閉的容器,裡面充滿著液壓油。在開關5關閉的情況下,當提起手柄時,小油缸1的柱塞上移使其工作容積增大形成部分真空,油箱6里的油便在大氣壓作用下通過濾網7和單向閥3進入小油缸;壓下手柄時,小油缸的柱塞下移,擠壓其下腔的油液,這部分壓力油便頂開單向閥4進入大油缸2,推動大柱塞從而頂起重物。再提起手柄時,大油缸內的壓力油將力圖倒流入小油缸,此時單向閥4自動關閉,使油不致倒流,這就保證了重物不致自動落下;壓下手柄時,單向閥3自動關閉,使液壓油不致倒流入油箱,而只能進入大油缸頂起重物。這樣,當手柄被反覆提起和壓下時,小油缸不斷交替進行著吸油和排油過程,壓力油不斷進入大油缸,將重物一點點地頂起。當需放下重物時,打開開關5,大油缸的柱塞便在重物作用下下移,將大油缸中的油液擠回油箱6。可見,液壓千斤頂工作需有兩個條件:一是處於密閉容器內的液體由於大小油缸工作容積的變化而能夠流動,二是這些液體具有壓力。能流動並具有一定壓力的液體具有壓力能。液壓千斤頂就是利用油液的壓力能將手柄上的力和位移轉變為頂起重物的力和位移。
傳動裝置的總體設計[3]
傳動裝置總體設計的任務是:確定傳動方案、選擇電動機型號、合理地分配傳動比及計算傳動裝置的運動和動力參數,為設計計算各級傳動零件提供依據。
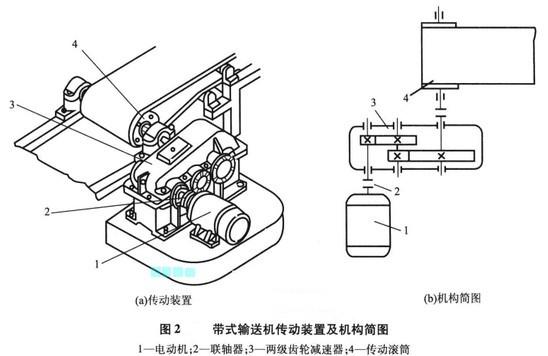
合理的傳動方案,應能滿足工作機的性能要求、工作可靠、結構簡單、尺寸緊湊、加工方便、成本低廉、效率高和使用維護方便等。要同時滿足這些要求,常常是困難的。因此,應統籌兼顧,確保重點要求。
但採用多級傳動時,應合理地選擇傳動零件和它們之間的傳動次序,揚長避短,力求方案合理。常需要考慮以下幾點。
(1)帶傳動為摩擦傳動,傳動平穩,能緩衝吸振,雜訊小,但傳動比不准確,傳遞相同轉矩時,結構尺寸較其他傳動形式大。因此,應佈置在高速級。因為在傳遞相同功率時,轉速越高,轉矩越小,可使帶傳動的結構緊湊。
(2)鏈傳動靠鏈輪齒嚙合工作,平均傳動比恆定,並能適應惡劣的工作條件,但運動不均勻,有衝擊,不適於高速傳動,故應佈置在低速級。
(3)蝸桿傳動平穩,傳動比大,但傳動效率低,適用於中、小功率及間歇運動的場合。當和齒輪傳動同時應用時,應佈置在高速級,使其工作齒面問有較高的相對滑動速度,利於形成流體動力潤滑油膜,提高效率,延長壽命。
(4)圓錐齒輪傳動由於圓錐齒輪加工比較困難(特別是尺寸較大時),應放在傳動的高速級,並限制其傳動比,以減小其直徑和模數。
(5)開式齒輪傳動的工作環境一般較差,潤滑不良,磨損嚴重,應佈置在低速級。
(6)斜齒輪傳動的平穩性較直齒輪傳動好,當採用雙級齒輪傳動時,高速級常用斜齒輪。
某些專業因受學時限制,傳動方案可在設計任務書中給出,不需學生選擇確定。但學生應對設計任務書給出的傳動裝置簡圖進行分析,瞭解傳動方案的組成和特點,以提高對傳動方案的選擇能力。
減速器是用於原動機和工作機之間的獨立的封閉裝置。由於減速器具有結構緊湊、傳動效率高、傳動準確可靠、使用維護方便等特點,故在各種機械設備中應用甚廣。
減速器的類型很多,用以滿足各種機械傳動的不同要求。其主要類型、特點及應用洋見濮良貴主編的《機械設計》第十八章內容。常用的減速器已標準化,由專門工廠成批生產。標準減速器的有關資料可查閱減速器標準,也可根據需要設計製造非標準減速器。
根據工作負荷的大小和性質、工作機的特性和工作環境等,選擇電動機的種類、類型和結構形式、功率及轉速,確定電動機的型號。
- 1.選擇電動機的種類、類型和結構形式
選擇電動機的種類、類型和結構形式要根據電源的種類(直流或交流)、工作條件(環境、溫度、空間位置等)及負荷性質、大小、啟動特性和過載情況等來選擇。
由於一般生產單位均用三相電源,故無特殊要求時都採用三相交流電動機。其中,以三相非同步電動機應用最多,常用Y系列電動機。經常啟動、制動和正反轉的場合,要求電動機具有較小的轉動慣量和較大的過載能力,因此,應選用冶金及起重用三相非同步電動機,常用YZ型(鼠籠式)或YZR型(繞線式)。電動機結構有開啟式、防護式、封閉式和防爆式等,可根據防護要求選擇。
- 2.選擇電動機的功率
電動機功率選擇是否合適,對電動機的工作和經濟性都有影響。功率過小不能保證工作機的正常工作,或使電動機因超載而過早損壞;若功率選得過大,電動機的價格高,能力不能充分發揮,經常不在滿載下運轉,效率和功率因數都很低,造成浪費。
電動機的功率主要根據工作機的功率來選取。負荷穩定(或變化很小)、長期連續運轉的機械可按照電動機的額定功率選擇,而不必校驗電動機的發熱和啟動轉矩。選擇時應保證
式中:P0——電動機額定功率,kW;
Pr——工作機所需電動機功率,kW。
所需電動機功率由式(2)計算
式中:Pw——工作機所需有效功率,kW;
η——電動機到工作機的總效率。
工作機所需有效功率由式(3)計算
式中:F——工作機的圓周力,N;
v——工作機的線速度,如運輸帶的帶速,m/s。
傳動裝置的總效率η由傳動裝置的組成確定。多級串聯傳動裝置的總效率為
式中:——傳動裝置中每x,-tN動副或傳動副(如聯軸器、齒輪傳動、帶傳動、滾動軸承及卷筒等)的效率。
計算總效率時,應註意以下幾點。
(1)各運動副或傳動副效率的概略值,可參見表1。表中數值是效率的範同,情況不明確時可取中間值;如果工作條件差,加工精度低,維護不良時,應取低值,反之取高值。
(2)動力每經過一個傳動副或運動副,就發生一次損失,故在計算效率時,不要遺漏。
(3)軸承的效率均指一對軸承而言。
表1 機械傳動效率概略值和傳動比範圍
類別 | 傳動型式 | 效率η | 單級傳動比範圍 | |
---|---|---|---|---|
最大 | 常用 | |||
圓柱齒輪傳動 | 7級精度(稀油潤滑) | 0.98 | ||
8級精度(稀油潤滑) | 0.97 | 10 | 3~5 | |
9級精度(稀油潤滑) | 0.96 | |||
開式傳動(脂潤滑) | 0.94~0.96 | 15 | 4~6 | |
錐齒輪傳動 | 7級精度(稀油潤滑) | 0.97 | 6 | 2~3 |
8級精度(稀油潤滑) | 0.94~0.97 | 6 | 2~3 | |
開式傳動(脂潤滑) | 0.92~0.95 | 6 | 4 | |
帶傳動 | V帶傳動 | 0.95 | 7 | 2~4 |
鏈傳動 | 滾子鏈(開式) | 0.90~0.93 | 7 | 2~4 |
滾子鏈(閉式) | O.95~0.97 | |||
蝸桿傳動 | 自鎖 | 0.40~0.45 | 開式100 | 15~16 |
單頭 | 0.70~O.75 | 閉式80 | 10~40 | |
雙頭 | 0.75~0.82 | |||
四頭 | 0.82~0.92 | |||
螺旋傳動 | 滑動絲杠 | 0.30~0.60 | ||
滾動絲杠 | O.85~0.90 | |||
一對滾動軸承 | 球軸承 | O.99 | ||
滾子軸承 | 0.98 | |||
一對滑動軸承 | 潤滑不良 | 0.94 | ||
正常潤滑 | 0.97 | |||
液體摩擦 | 0.99 | |||
聯軸器 | 齒式聯軸器 | 0.99 | ||
彈性聯軸器 | O.99~0.995 | |||
運輸滾筒 | 0.96 |
- 3.確定電動機的轉速
選擇電動機,除了選擇合適的電動機系列及功率外,尚需確定適當的轉速。因為功率相同的同類電機,可以有不同的轉速,如三相非同步電動機的同步轉速有3000 r/min、1500 r/min、1000 r/min及750 r/min四種。一般說來,高速電動機的磁極對數少,結構較簡單,外廓尺寸小,價格低。但電動機轉速相對工作機轉速過高時,勢必使傳動比增大,致使傳動裝置複雜,外廓尺寸增大,製造成本提高。而選用的電動機轉速過低時,優缺點剛好相反。因此,在確定電動機轉速時,應分析比較,權衡利弊,按最佳方案選擇。本課程設計中,一般建議取同步轉速為1000 r/min或1500 r/min,個別題目可取750 r/min。
【1】如圖2所示膠帶輸送機,運輸帶的有效拉力F=1500N,帶速v=1.6m/s,卷筒直徑D=250 mm,載貨平穩,常溫下連續運轉,工作環境多塵,電源為三相交流,電壓為380V,試選擇電動機。
【解】(1)選擇電動機系列。按工作要求及工作條件選擇三相非同步電動機,封閉式結構,Y系列。
(2)選擇電動機功率。卷筒所需的有效功率為
按表1選取得
η齒輪=0.97(齒輪精度為8級)
η聯軸器=0.99
η軸承=0.99
η捲簡=0.96
則傳動總效率為
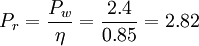
所需電動機功率可選Y系列三相非同步電動機Y100L2—4型,額定功率P0 = 3kW,或選Y系列二三相非同步電動機Y132S—6型,額定功率P0 = 3kW。
(3)確定電動機轉速。滾筒軸轉速為
現以同步轉速為1500 r/min及1000 r/min兩種方案進行比較,其電動機數據及計算出的總傳動比列於表2。
表2 電動機數據及總傳動比
方案號 | 電動機型號 | 額定功率kW | 同步轉速/(r/min) | 滿載轉速/(r/min) | 總傳動比 |
---|---|---|---|---|---|
1 | Y100L2-4 | 3 | 1500 | 1420 | 11.61 |
2 | Y132S-6 | 3 | 1000 | 960 | 7.85 |
比較兩方案可見,方案2雖然總的傳動比小,但選用電動機的質量和價格較高,敝決定選擇方案1。電動機的型號為Y100L2-4,額定功率為3kW,同步轉速為1500 r/min,滿載轉速為1420 r/min。查得電動機的中心高H=100 mm,外伸軸段D×E=28 mm×60 mm。
- 4.分配總的傳動比


當設計多級傳動的傳動裝置時,分配傳動比是一個重要的步驟。往往由於傳動比分配不當,造成尺寸不緊湊、結構不協調、成本高、維護不便等問題。欲做到較合理地分配傳動比應註意以下幾點。
(1)各級傳動比均應在合理的範圍內,以符合各種傳動形式的特點,使結構緊湊、工藝合理。各種傳動的傳動比薦用值列於表1。
(2)傳動裝置中各級傳動間應尺寸協調、結構勻稱。例如,在由帶傳動和單級齒輪傳動組成的雙級傳動中,帶傳動的傳動比不宜過大,一般應使i帶<i齒,這樣,不僅可以使傳動裝置結構緊湊,又能避免當帶傳動比過大時,由大帶輪的外圓半徑大於減速器中心高H所造成的安裝困難,如圖3所示。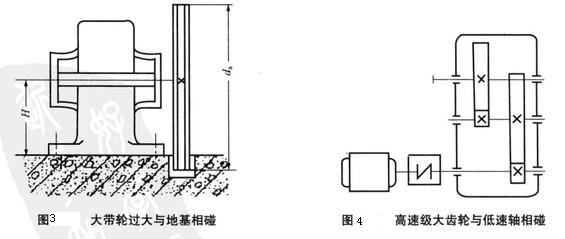
(3)各傳動件彼此不發生干涉碰撞。例如,在雙級圓柱齒輪減速器中,若高速級傳動比過大,可能會使高速級大齒輪的齒頂圓與低速級大齒輪的軸相碰,如圖4所示。
(4)當設計展開式的兩級圓柱齒輪減速器時,為便於油池潤滑,應使高速級和低速級大齒輪的浸油深度大致相近。為此傳動比可按式(6)分配
式中:i1,i2——高速級和低速級的傳動比;
ijian——減速器的傳動比。
【例2】數據同例1,選定電動機的滿載轉速n0=1420 r/min,總傳動比i=1420/122.3=11.61,試分配各級傳動比。
【解】取兩級齒輪減速器高速級的傳動比
要註意,以上傳動比的分配只是初步的。傳動裝置實際傳動比的準確數值必須在各傳動零件的參數(如帶輪直徑、齒輪齒數等)確定後才能計算出來,故實際傳動比應在各傳動零件的參數確定後進行核算。允許傳動比有±(3~5)%的誤差。
- 5.傳動裝置的運動和動力參數計算
在選出電動機型號、分配傳動比之後,應將傳動裝置中各軸的傳遞功率、轉速、轉矩計算出來,為傳動零件和軸的設計計算提供依據。計算時應註意:
(1)各軸的轉速可根據電動機的滿載轉速及傳動比進行計算。
(2)各軸的功率和轉矩均按輸入處計算,計算過程中有兩種方法:其一是按工作機的需要計算;其二是按電動機的額定功率計算。前一種方法的特點是,設計出的傳動裝置結構尺寸較為緊湊;而後一種方法,由於一般所選定的電動機額定功率P0略大於工作機所需電動機功率Pr,故根據P0計算出的各軸功率和轉速較實際需要的大一些,設計出的傳動零件的結構尺寸也較實際需要大一些,因此傳動裝置的承載能力對生產具有一定的潛力。
計算時,將傳動裝置中各軸從高速到低速依次定為I軸、Ⅱ軸……(電動機為0軸),相鄰兩軸間的傳動比為i12,i23,…,相鄰兩軸問的傳動效率為η12,η23,…,各軸的輸入功率為P1,P2,…,各軸的轉速為n1,n2,…,各軸的輸入轉矩為T1,T2,…,則各軸的功率、轉速和轉矩的計算公式為


式中:P0——電動機軸的輸出功率,kW;
n0——電動機軸的滿載轉速,r/min;
T0——電動機軸的輸出轉矩,N·m;
i01——電動機軸至I軸的傳動比,如用聯軸器連接,則i01 = 1;
η01——電動機軸至I軸的傳動效率。
若按第一種方法計算時,P0為工作機所需的電動機功率,即P0 = Pr;若按第二種方法計算,P0即為電動機的額定功率。本課程設計要求按第一種方法計算。
【例3】數據同例1及例2,試從電動機開始計算各軸運動和動力參數。
【解】0軸:0軸即電動機軸
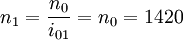






將上述計算結果彙總列於表3,以便查用。
表3 各軸運動和動力參數
軸序號 | 功率P/kW | 轉速n/(r/min) | 轉矩T | 傳動形式 | 傳動比i | 效率η |
---|---|---|---|---|---|---|
0 | 2.82 | 1420 | 18.97 | 聯軸器 | 1 | 0.99 |
I | 2.79 | 1420 | 18.76 | 齒輪傳動 | 3.88 | 0.97 |
Ⅱ | 2.68 | 365.98 | 69.93 | 齒輪傳動 | 3.0 | 0.97 |
Ⅲ | 2.57 | 121.99 | 201.19 | 聯軸器 | 1 | 0.99 |
Ⅳ | 2.52 | 121.99 | 196.28 | 滾筒 | - | 0.96 |