机械零件
出自 MBA智库百科(https://wiki.mbalib.com/)
机械零件(Machine Part)
目录[隐藏] |
什么是机械零件[1]
机械零件是指组成机器的不可拆分的基本单元,如螺栓、螺钉、键、带、齿轮、轴、弹簧、销等。
机械零件的分类[1]
通用零件是指能在各种机器中广泛使用的零件,专用零件是指只能在某一类特定的机器中使用的零件。
机械零件的材料[2]
一、机械零件常用材料
机械零件的材料有金属材料、非金属材料和复合材料。
金属材料分为黑色金属材料和有色金属材料。黑色金属材料包括各种钢、铸钢和铸铁,具有较好的力学性能(如强度、塑性、韧性等),价格相对便宜且容易获得,而且能满足多种性能和用途的要求。在各类黑色金属中,由于合金钢的性能优良,因而常常用来制造重要的零件。有色金属材料包括铜合金、铝合金、轴承合金等,具有密度小、导热和导电性能好等优点,通常还可用于有减摩、耐磨及耐腐蚀要求的场合。
非金属材料指塑料、橡胶、合成纤维等高分子材料及陶瓷等。高分子材料有许多优点,如原料丰富、密度小,在适当的温度范围内有很好的弹性,耐腐蚀性好等。其主要缺点是容易老化,其中不少材料阻燃性差,总体上讲,耐热性不好。陶瓷材料的主要特点是硬度极高、耐磨、耐腐蚀、熔点高、刚度大以及密度比钢铁小等。目前,陶瓷材料已应用于密封件、滚动轴承和切削刀具等结构中。其主要缺点是比较脆,断裂韧度低,价格昂贵,加工工艺性差等。
复合材料是指用两种或两种以上具有明显不同的物理和力学性能的材料经复合工艺处理而得到所需性能的一种新型材料。例如用玻璃、石墨(碳)、硼、塑料等非金属材料可以复合成各种纤维增强复合材料。在普通碳素钢板表面贴附塑料,可以获得强度高而又耐腐蚀的塑料复合钢板,主要优点是有较高的强度和弹性模量,而质量又特别小,但也有耐热性差、导热和导电性能较差的缺点。此外,复合材料的价格比较贵。所以目前复合材料主要用于航空、航天等高科技领域,在民用产品中,复合材料也有一些应用。
二、机械零件材料选择原则
从各种各样的材料中选择出适用的材料,是一项受多方面因素所制约的工作。在以后的有关章节中,将分别介绍各种零件适用的材料和牌号。下面就金属材料(主要是钢铁)的一般选用原则作一简介。
选择机械零件材料的原则是:所需材料应满足零件的使用要求,有良好的工艺性和经济性等。
1.使用要求
机械零件的使用要求表现为以下几点:
(1)零件的工作状况和受载情况,以及为避免相应的失效形式而提出的要求工作状况是指零件所处的环境特点、工作温度、摩擦和磨损的程度等。在湿热环境或腐蚀介质中工作的零件,其材料应有良好的缓蚀和耐腐蚀的能力,例如选用不锈钢、铜合金等。工作温度对材料选择的影响,一方面要考虑互相配合的两零件的材料的线胀系数不能相差过大,以免在温度变化时产生过大的热应力或者使配合松动;另一方面也要考虑材料的力学性能随温度而改变的情况。在滑动摩擦下工作的零件,要提高其表面硬度,以增强耐磨性,应选择适于进行表面处理的淬火钢、渗碳钢、氮化钢等品种或选用减摩和耐磨性能好的材料。
受载情况是指载荷、应力的大小和性质。脆性材料原则上只适用于制造在静载荷下工作的零件;在多少有些冲击的情况下,应以塑性材料作为主要使用的材料;对于表面受较大接触应力的零件,应选择可以进行表面处理的材料,如表面硬化钢;对于受变应力的零件,应选择耐疲劳的材料;对于受冲击载荷的零件,应选择冲击韧度较高的材料;对于尺寸取决于强度,且尺寸和质量又受限的零件,应选择强度较高的材料;对于尺寸取决于刚度的零件,应选用弹性模量较大的材料。
金属材料的性能一般可通过热处理加以提高和改善,因此,要充分利用热处理的手段来发挥材料的潜力。对于最常用的调质钢,由于其回火温度的不同,可得到力学性能不同的毛坯。回火温度越高,材料的硬度和强度将越低,而塑性越好。所以在选择材料的品种时。应同时规定其热处理规范,并在图样上加以注明。
(2)对零件尺寸和质量的限制零件尺寸及质量的大小与材料的品种及毛坯制取方法有关。用铸造材料制造毛坯时,一般可以不受尺寸及质量大小的限制;而用锻造材料制造毛坯时,则需注意锻压机械及设备的生产能力。此外,零件尺寸和质量的大小还和材料的强重比有关,应尽可能选用强重比大的材料,以便减小零件的尺寸和质量。
(3)零件在整机或部件中的重要程度。
2.工艺要求
要考虑所用的材料从毛坯到成品都能方便地制造出来。例如,结构复杂、尺寸较大的零件难以锻造,可以采用铸造或焊接,其材料必须具有良好的铸造性能或焊接性能。
根据所选的工艺,要考虑材料对该工艺的加工可能性。对于铸造,要考虑材料的液态流动性、产生缩孔和偏析的可能性等;对于焊接,要考虑材料的焊接性和产生裂纹的倾向等;对于锻造,要考虑材料的延伸性、热脆性和变形能力等;对于需要热处理的零件,要考虑材料的淬透性、淬火变形的倾向性等;对于需经切削加工的零件,要考虑材料的硬度、易切削性、冷作硬化程度和切削后能达到的表面粗糙度等。
3.经济要求
(1)材料本身的相对价格在满足使用要求的前提下,应尽量选用价格低廉的材料。这一点对于大批量制造的零件尤其重要。
(2)材料的加工费用当零件质量不大而加工量很大时,加工费用在零件总成本中要占很大比例。尽管铸铁比钢板价廉,但对于某些单件或小批量生产的箱体类零件来说,采用铸铁反而比采用钢板焊接的成本更高,因为后者可以省掉模具的制造费用。
(3)材料的利用率采用无屑或少切屑加工,如模锻、精铸、冲压等,可以提高材料的利用率。
(4)局部品质原则在很多情况下,零件在其不同的部位上对材料有不同的要求。要想选用一种材料满足不同的要求,事实上是不可能的,即使可能,价格也非常昂贵。这时,可根据局部品质原则,在不同的部位上采用不同的材料或采用不同的热处理工艺,使各局部的要求分别得到满足。例如蜗轮的轮齿必须具有优良的耐磨性和较高的抗胶合能力,其他部分只需具有一般的强度即可,故在铸铁轮芯外套用青铜齿圈,以满足这些要求。又如滑动轴承只在其和轴颈接触的表面处要求有减摩性,所以只需用减摩材料制成轴瓦,而不必把整个轴承都用减摩材料制造。
局部品质也可以用渗碳、表面淬火、表面喷镀、表面辗压等方法获得。
(5)材料代用以节约贵重、稀有材料由于供应上的原因或经济性的要求,可以对所选材料用其他材料代用。例如,当强度为主要要求时,可选用强度较高而价格较贵的材料,也可用强度较差而价廉的材料代替,而将结构尺寸适当加大;当耐磨或耐腐蚀为主要要求时,可以不选用耐磨性或防腐性好的材料而选用较差的材料进行各种表面硬化处理或防腐处理;对于稀有材料,也可以用普通材料代替,例如用铝青铜代替锡青铜制造轴瓦。
(6)材料供应情况从简化材料品种的供应和储存出发,对于小批量生产的零件,应尽可能减少同一台机器上使用材料的品种和规格。
机械零件的设计方法[3]
一、机械零件的常规设计方法
1.理论设计
理论设计是根据设计理论和实验数据所进行的设计。它又可分为设计计算和校核计算两类。设计计算是根据零件的工作情况,选定计算准则,按其所规定的要求计算出零件的主要几何尺寸和参数。校核计算是先按其他办法初步拟定出零件的主要尺寸和参数,然后根据计算准则所规定的要求校校零件是否安全。由于校核计算时,已知零件的有关尺寸,因此能计入影响强度的结构因素和尺寸因素,计算结果比较精确。
2.经验设计
经验设计是根据已有的经验公式或设计者本人的工作经验,或借助类比方法所进行的设计。这主要适用于使用要求不大变动而结构形状已典型化的零件,如箱体、机架、传动零件的结构要素等。
3.模型实验设计
这种设计是对一些尺寸巨大、结构复杂的重要零件,根据初步设计的结果,按比例制成小尺寸的模型,经过实验手段对其各方面的特性进行检验,再根据实验结果对原设计进行逐步修改,从而达到完善的设计。模型实验设计是在设计理论还不成熟,已有的经验又不足以解决设计问题时,为积累新经验、发展新理论和获得好结果而采用的一种设计方法。但这种设计方法费时、耗资,一般只用于特别重要的设计中。
二、机械零件设计的一般步骤
1)选择零件的类型和结构。这要根据零件的使用要求,在熟悉各种零件的类型、特点及应用范围的基础上进行。
2)分析和计算载荷。分析和计算载荷,是根据机器的工作情况,来确定作用在零件上的载荷。
3)选择合适的材料。要根据零件的使用要求、工艺要求和经济性要求来选择合适的材料。
4)确定零件的主要尺寸和参数。根据对零件的失效分析和所确定的计算准则进行计算,便可确定零件的主要尺寸和参数。
5)零件的结构设计。应根据功能要求、工艺要求、标准化要求,确定零件合理的形状和结构尺寸。
6)校核计算。只是对重要的零件且有必要时才进行这种校核计算,以确定零件工作时的安全程度。
7)绘制零件的工作图。
8)编写设计计算说明书。
三、机械零件的设计计算
机械零件的主要尺寸常常需要通过理论计算确定。理论设计计算是根据零件的结构特点和工作情况,将它合理简化成一定的物理模型,运用理论力学、材料力学、流体力学、摩擦学、热力学、机械振动学等理论或利用这些理论推导出设计公式、实验数据来进行设计。理论设计计算可分为设计计算和校核计算两种。
1)设计计算。按设计公式直接求得零件的有关主要尺寸。
2)校核计算。已知零件各部分的尺寸,用设计公式校核它是否满足有关的设计计算准则。
为了使设计计算的结果更符合实际,应该多方面参考过去成功的设计和实践积累的经验关系式、统计数据等。对于一些大型、结构复杂的重要零件,必要时还可以进行模型实验或实物实验。
机械零件设计中的工艺性及标准化[2]
一、工艺性
良好的工艺性是指所设计的机械零件能用最短的时间、最少的劳动量、最低的制造费用生产出来,且装拆、维修方便。零件制造一般包括毛坯生产、切削加工、热处理、装配等阶段,各阶段都是有机联系着的,设计时必须全面考虑。设计机械零件时有关工艺性的基本要求有以下几方面的内容:
1.零件的结构与生产条件和规模相适应
单件或小批量生产的零件,应充分利用现有的生产条件。如直径大于600mm的齿轮毛坯,用一般的锻压设备难以锻造,应采用铸件或焊接件。在单件或小批量生产时,不宜采用铸件或模锻件,以免模具造价太贵(尤其是模锻)而提高零件成本。如果没有磨齿机床,就不要采用齿面硬度高、热处理变形大的热处理方法。
2.毛坯选择合理
零件的毛坯可以是铸件、锻件、轧制件、焊接件和冲压件等。毛坯的选择应考虑生产批量大小、材料性能和加工性能等。如对锻件而言,单件或小批量生产宜用自由锻,大批量生产宜用模锻。
3.结构和形状应简单合理
零件的结构和形状越复杂,制造、装配和维修就越困难,成本也就越高,因此,要尽可能采用简单的圆柱面、平面、共轭曲面及其组合,尽量减少被加工面的数目和被加工面的面积,尽量采用相同尺寸(直径、圆角半径、配合尺寸和公差,螺纹的直径、线数和螺距,齿轮模数等)。
4.规定合理的制造精度和表面粗糙度
制造精度过高、表面粗糙度值过低,都会明显增加机械零件的制造成本。因此,在满足使用要求的前提下,应尽可能降低制造精度、增大表面粗糙度值。
5.满足热处理的要求
为避免热处理时变形、开裂或降低热处理质量(如硬度不足、软点、强度低、渗碳层薄或不均匀等),零件的几何形状应简单、对称,长径比不可太大,尽量减少应力集中源,截面均匀,无锐边和尖角,避免不通孔、配作孔和局部渗碳、渗氮等。零件也应有足够的刚度。为使淬火气膜不易附着、冷却均匀、变形较小,对零件表面粗糙度有一定要求。
6.考虑装拆的工艺性
设计中,应考虑零件能便于装配、拆卸,并尽可能减少装拆的工作量,还应考虑搬运、安装、使用、维修的方便性和经济性。
二、标准化
标准化是指对零件的尺寸、结构要素、材料性能、检验方法、设计方法、制图要求等制定出各式各样的标准,供大家共同遵守。与标准化密切相关的是零部件的通用化、产品的系列化。
通用化是指最大限度地减少和合并产品的形式、尺寸和材料的品种,使零部件尽量在不同规格的同类产品乃至不同类产品中通用,以减少企业内部的零部件种数,从而简化生产管理,并获得较高的经济效益。
系列化是指将尺寸和结构拟订出一定数量的原始模型,然后根据需求,按照一定的规律优化组合成产品系列。
标准化、通用化和系列化被统称为“三化”。“三化”的优越性表现在:
1)采用标准结构及零部件,可以简化设计工作,缩短设计周期,提高设计质量。
2)便于安排专门工厂采用先进技术进行专业化大生产,保证产品质量,并能大幅度降低劳动量、材料消耗和制造成本。
3)技术条件和检验、试验方法的标准化,可以改进和提高零部件的质量。
4)增强互换性,便于维修。
我国现已颁布的与机械设计有关的标准,可以分为国家标准(GB、GB/T)、部颁标准(如JB、YB等)、专业标准和企业标准四级。我国已加入国际标准化组织(ISO),许多新的国家标准已采用了相应的国际标准。设计时,应执行和采用各项标准。
机械零件设计的注意事项[4]
产品设计过程是智力活动过程,它体现了设计人员的创新思维活动,设计过程是逐步逼近解决方案并逐步完善的过程。设计过程中还应注意以下几点。
(1)设计过程要有全局观点,不能只考虑设计对象本身的问题,而要把设计对象看作一个系统,处理“人—机—环境”之间的关系。
(2)善于运用创造性思维和方法,注意考虑多种方案的解,避免解决问题的局限性。
(3)设计的各阶段应有明确的目标,注意各阶段的评价和优选,以求出既满足功能要求又有最大实现可能的方案。
(4)要注意反馈及必要的工作循环。解决问题要由抽象到具体,由局部到全面,由不确定到确定。
机械零件的强度[5]
一、载荷和应力
1.载荷
载荷是指零件或构件工作时所承受的外力。根据载荷性质的不同,可分为静载荷和变载荷两类。
·不随时间变化或变化较缓慢的载荷称为静载荷,如重力,锅炉中的压力,螺栓拧紧后受到的拉力;
·随时间变化的栽荷称为变载荷,如内燃机活塞杆受到的力,机器中的齿轮受到的力等。
在计算中,将载荷分为名义载荷和计算载荷。
·根据原动机额定功率(或阻力、阻力矩)计算出来的作用于机械零件上的载荷称为名义载荷,一般用F表示力,用T表示力矩。
·考虑机械零件在工作时有冲击、振动和由于各种因素引起的栽荷分布不均匀等.将名义载荷修正后用于零件计算的栽荷称为计算载荷,以Fc,Tc表示。
计算载荷与名义载荷的关系为:式中,K为载荷系数,一般取K≥1。
2.应力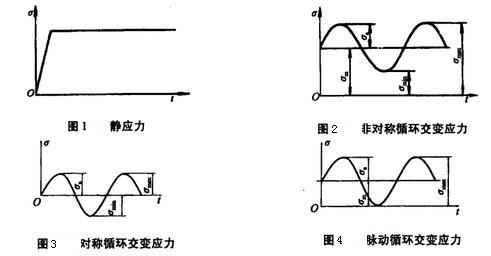
与载荷一样,构件内的应力也分为两类:静应力和变应力。
·在静载荷作用下产生的不随时间变化的应力称为静应力,如图1所示;
·在变栽荷作用下(或静栽荷作用在运动的零件上)产生的随时间变化的应力称为变应力,如果应力随时间做周期性的变化则称为交变应力。
根据应力随时间变化的规律,较典型的交变应力有:非对称循环的交变应力(如图2所示)、对称循环的交变应力(如图3所示),脉动循环的交变应力(如图4所示)。
如图2所示,交变应力的最大应力为σmax,最小应力为σmin时,其平均应力σm和应力幅σa分别为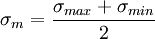
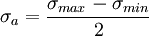

由上述可知,交变应力参数共有5个,即σmin、σmax、σm、σa和r,已知其中两个参数便可求出其余参数。循环特征r可以用来表示应力的变化情况,对称循环的交变应力,r=-1;脉动循环的交变应力,r=O;非对称循环的交变应力,r随具体受力情况不同在-1~+1之间变化:静应力则可看作交变应力的一个特例,即r=+1。
二、零件的极限应力σlim
1.静应力下的极限应力
在静应力下工作的机械零件,其极限应力σlim取决于零件的失效形式。
·对于脆性材料制成的零件应防止发生断裂,通常取材料的强度极限σB作为极限应力,即σlim = σB;
·当采用塑性材料制成零件时,应防止产生过大的塑性变形,通常取材料的屈服极限σa作为极限应力,即σlim = σa。
2.交变应力下的极限应力
在交变应力下长期工作的零件,其σlim抽取决于材料的疲劳断裂,而疲劳断裂是一种损伤积累,它会在远低于强度极限的应力下,突然断裂而无明显的塑性变形,这时的应力称为疲劳极限(或称持久极限)。
如图5所示是表示应力σ和应力循环次数N之间关系的疲劳曲线。从图中可以看出,应力愈小,零件材料能经受的应力循环次数也就愈多。对于一般钢铁来说,当循环次数N超过某一值No以后,曲线趋向于水平,即N>No时,疲劳极限N不再随循环次数的增加而降低。No称为循环基数,对应于No的应力称为材料的持久极限。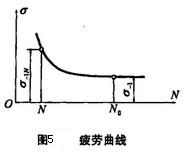
在对称循环交变应力下,r=-1,取其持久极限σ1,作为极限应力;在脉动循环交变应力下,r=0取其持久极限σ0作n为极限应力。
三、机械零件的强度计算
强度是指零件抵抗破坏的能力,是保证机械零件工作能力的最基本要求。如果零件的强度不够,不仅会因零件的失效而使机器不能正常工作,甚至还可能导致安全事故。
零件的强度分为体积强度和表面接触强度。
·零件在栽荷作用下,如果产生的应力在较大的体积内,这种应力状态下的零件强度称为体积强度(通常简称强度)。
·若两零件在受载前后由点接触或线接触变为小表面积接触,而且其表面产生很大的局部应力(称为接触应力),这时零件的强度称为表面接触强度(简称接触强度)。
若零件的强度不够,就会出现整体断裂。表面接触疲劳或塑性变形等失效而丧失工作能力。所以,设计零件时,必须满足强度要求。强度计算准则为
σ≤[σ]或τ≤[τ]
[σ]=;[τ]=
式中,σ、τ——零件工作时的正应力和切应力;
[σ]、[τ]——零件材料的许用正应力和许用切应力。
S、Sτ ——正应力和切应力的安全系数;
σlim、τlim——材料的极限正应力和极限切应力。
机械零件的失效[6]
机械零件的失效是指零件在使用过程中,零件部分或完全丧失了设计功能。零件完全被破坏不能继续工作;或零件已严重损坏,若继续工作将失去安全;或虽能安全工作,但已失去设计精度等现象都属于失效。
为了预防零件失效,需对零件进行失效分析,即通过判断零件失效形式、确定零件失效机理和原因,有针对性地进行选材、确定合理的加工路线,提出预防失效的措施。
1.机械零件失效形式
机械零件常见的失效方式可以分为三种类型:过量变形失效、断裂失效和表面损伤失效。
(1)过量变形失效:零件因变形量过大超过允许范围而造成的失效。它主要包括过量弹性变形、塑性变形和高温下发生的蠕变等失效形式。
(2)断裂失效:因零件承载过大或疲劳损伤等原因而导致分离为互不相连的两个或两个以上部分的现象。断裂是最严重的失效形式,它包括韧性断裂失效、低温脆性断裂失效、疲劳断裂失效、蠕变断裂失效和环境破断失效等几种形式。
(3)表面损伤失效:零件工作时由于表面的相对摩擦或受到环境介质的腐蚀在零件表面造成损伤或尺寸变化而引起的失效。它主要包括表面磨损失效、腐蚀失效、表面疲劳失效等形式。
需要指出,同一种机械零件在工作中往往不只是一种失效方式起作用。但是,一般造成零件失效时总是一种方式起主导作用。失效分析的核心问题就是要找出主要的失效方式。
2.机械零件失效的原因
引起机械零件失效的因素很多且较为复杂,涉及零件的结构设计、材料选择、材料的加工制造、产品的装配及使用保养等多个方面。
(1)设计不合理:主要是指零件结构和形状不正确或不合理,如零件存在缺口、小圆弧转角、不同形状过渡区等。另一方面是指对零件的工作条件、过载情况估计不足,造成零件实际工作能力不足,致使零件早期失效。
(2)选材不合理:设计中对零件失效的形式判断错误,所选的材料性能不能满足工作条件需要;选材所依据的性能指标不能反映材料对实际失效形式的抗力,选择了错误的材料;所选用的材料质量太差,成分或性能不合格导致不能满足设计要求等都属于选材不合理。
(3)加工工艺不合理:零件的加工工艺不当,可能会产生各种缺陷,导致零件在使用过程中较早地失效。如热加工过程中出现过热、过烧和带状组织;热处理过程中出现脱碳、变形、开裂;冷加工过程出现较深的刀痕、磨削裂纹等。
(4)安装使用不当:装配和安装过程不符合技术要求,如安装时配合过紧、过松,对中不准,固定不稳等都可能导致零件不能正常工作或过早出现失效;此外,使用过程中违章操作、超载、超速、不按时维修和保养等也会造成零件过早出现失效。