不良品
出自 MBA智库百科(https://wiki.mbalib.com/)
目录[隐藏] |
什么是不良品[1]
不良品是指不符合产品质量标准或订货合同规定的技术要求的产品。
不良品的分类[1]
不良品按其不合格的程度可分为:返修品、回用品、次品和废品等。
(1)返修品:指产品或零件不符合产品图纸和工艺规程的技术要求,但通过修理,有可能达到合格要求的不合格品。
(2)回用品:指产品或零件不合格,但其缺陷的项目和超差数值对产品的性能、寿命、安全性、可靠性、互换性及用户的正常使用均无明显影响,可由生产部门或责任单位提出回用申请报告,经有关部门审批同意回用的不合格品。
(3)次品:指产品或零件不合格,但还具有使用价值,经有关部门会签,企业主管批准,可以降等或降价处理的不合格品。
(4)废品:指产品或零件不合格,且不能修复,又不能回用,必须废弃的不合格品。
不良品产生的原因[1]
造成不良品产生的原因很多,难以一一罗列,摘其主要的原因如下:
(1)由于产品开发设计产生的有:
①采用的质量标准不准确或不完善;
②产品设计图样、图纸绘制不规范,不清晰,标码不准确;
③设计图纸、技术文件废弃、更换和修改等管理不善,造成加工过程中误用、乱用。
(2)由于工艺编制和控制产生的有:
①工艺编制、审校不严而发生的选用设备、工、夹、量、刃具不当或工装设计有差错;
②选用的工艺基面不当,造成与设计基面不协调;
③工艺编写不规范,尺寸、公差标注不清晰,如易发生“b”与“6”相混淆差错;
④工艺规程修改不规范,如只改尺寸、公差标准,不改图形。
⑤现场在用的旧工艺已油污、破损、模糊不清,不及时更换,易发生看错。
(3)由于设备和检测器具管理产生的有:
①设备的维修、保养不当,造成设备精度走失;
②设备安装、调试不当或设备的加工能力不足;
③量具、量仪的测量能力不足;
④量具、量仪未按周期检修或维护保养不当,造成测量误差大。
(4)由于材料与配件管理产生的有:
①使用已长期存放变异的原材料或配件;
②材料或配件领发错了;
③使用让步接收的材料或配件;
④代用材料选用不当;
(5)由于生产作业管理产生的有:
①生产管理人员重产量、轻质量,指挥失误;
②操作人员思想和技术素质低或未经培训上岗;
③操作员工缺乏自主管理质量意识。
(6)由于检验员漏检产生的有:
①检验员思想和技术素质低或未经培训上岗;
②检验员粗心大意或质量意识差;
③技术标准、图纸和工艺不完善,含糊不清,使检验员造成误判。
不良品的标识[2]
为了确保不良品在生产过程中不被误用,工厂所有的外购货品、在制品、半成品、成品以及待处理的不良品均应有品质识别标识。
1.选择标识物
(1)标识牌。它是由木板或金属片做成的小方牌,按货品属性或处理类型将相应的标识牌悬挂在货物的外包装上加以标示。
根据企业标识需求,可分为“待验牌”、“暂收牌”、“合格牌”、“不合格牌”、“待处理牌”、“冻结牌”、“退货牌”、“重检牌”、“返工牌”、“返修牌”、“报废牌”等。标识牌主要适用于大型货物或成批产品的标示。
(2)标签或卡片。该标识物一般为一张标签纸或卡片,通常也称之为“箱头纸”。在使用时将货物判别类型标注在上面,并注明货物的品名、规格、颜色、材质、来源、工单编号、日期、数量等内容。在标示品质状态时,质检员按物品的品质检验结果在标签或卡片的“品质”栏盖相应的Q C标示印章。
(3)色标。色标的形状一般为一张正方形(2厘米×2厘米)的有色粘贴纸。它可直接贴在货物表面规定的位置,也可贴在产品的外包装或标签纸上。色标的颜色一般分为:绿色、黄色、红色三种(如表1所示)。
表1 色标所代表意义及贴置位置
绿色 | 代表受检产品合格 | 一般贴在货物表面的右下角易于看见的地方 |
黄色 | 代表受检产品品质暂时无法确定 | 一般贴在货品表面的右上角易于看见的地方 |
红色 | 代表受检产品不合格 | 一般贴在贷物表面的左上角易于看见的地方 |
2.不良品标识要求
在生产现场的每台机器旁,每条装配拉台、包装线或每个工位旁边一般应设置专门的“不良品箱”。
(1)对员工自检出的或班组长在巡检中判定的不良品,班组长则应让员工主动地将其放入“不良品箱”中,待该箱装满时或该工单产品生产完成时,由专门员工清点数量。
(2)在容器的外包装表面指定的位置贴上“箱头纸”或“标签”,经所在部门的质检员盖“不合格”字样或“REJECT”印章后搬运到现场划定的“不合格”区域整齐摆放。
不良品的隔离[2]
对经过标示的不良品应放置在有隔离措施的场所,这些隔离措施应能保证可以容易地被识别,或不易被错误使用。
1.不良品区域
在各生产现场(制造/装配或包装)的每台机器或拉台的每个工位旁边,均应配有专用的不良品箱或袋,以便用来收集生产中产生的不良品。
在各生产现场(制造/装配或包装)的每台机器或拉台的每个工位旁边,要专门划出一个专用区域用来摆放不良品箱或袋,该区域即为“不良品暂放区”。
各生产现场和楼层要规划出一定面积的“不良品摆放区”用来摆放从生产线上收集来的不良品。
所有的“不良品摆放区”均要用有色油漆进行画线和文字注明,区域面积的大小视该单位产生不良品的数量而定。
2.标识放置
(1)对已做过判定的不良品,所在班组或责任人员无异议时,由责任班组安排人员将不良品集中打包或装箱。质检员在每个包装物的表面盖“REJECT”印章后,由班组现场人员送到“不良品摆放区”,按类型堆栈、叠码。
(2)对质检员判定的不良品,责任班组有异议时,由班组长向所本部门的质检组长以上级别的品质管理人员进行交涉,直至异议公平、公正解决为止。
3.不良品区域管制
(1)不良品区内的货物,在没有品质部的书面处理通知时,任何部门或个人不得擅自处理或运用不良品。
(2)不良品的处理必须耍由品质部临督进行。
4.不良品记录
现场班组长或质检员应将当天产生的不良品数量如实地记录在当天的巡检报表上,同时对当天送往“不合格区”的不良品进行分类,详细地填写在“不良品隔离控制统计表”(该表应注明负责班组、工位、不良品变动情况、生产区编号等)上,并经生产部门或班组签认后交品质部存查。
不良品的处理[3]
1.处理步骤
不良品是万恶之首。管理的历史可以说就是一部与不良品作斗争的历史。只要有生产活动存在,就有不良品的存在。不良品是测试管理人员合格与否的最好“考题”之一,谁也躲不开。但是,面对同一种不良品现象,其原因却是多样的,有的可以借助以往的经验,一眼看穿,有的要依靠解析手段来找出原因。解析时,一般要遵循以下步骤。
第一步:再现不良现象。
尽可能从多方面观察不良现象,若有数据,则需记录下来。
第二步:调查原因。
1)模拟法。使用相同组合的生产要素,确认能否导致同一不良现象。
2)配对法。将生产要素按一定的条件进行组合,确认哪种组合会出现相同的不良品。
3)排除法。将生产要素逐个进行替换,当替换到不良品消失时,多半是该生产要素引发的不良现象。
4)对比法。将良品与不良品进行比较,找出其中差别之处,这种差别很可能就是造成不良的原因。
2.注意事项
以上这些方法只不过是将导致不良的生产要素找出来,为对策铺垫了基础,但这还不够,还要给予反证才行,尤其在理论计算时,要注意以下事项。
1)尽可能使用高精度的测试仪器测取数据。
2)审图、读取数据时不偏不倚,不人为地改动数据。
3)当运算公式、方程式时,再三确认有无代入错误。
在不良原因查明之后,便要进行对策,不良对策不是简单地下一道加工、选别、修理的指示,而是要制定整体的挽救方法、日程、担当者。根据不良品评审所做出的决定,对不良品要立即采取相应的处置措施。关于不良品的性质以及随后所采取的措施,包括所需的标准均应加以记录。不良品处理流程如图1所示。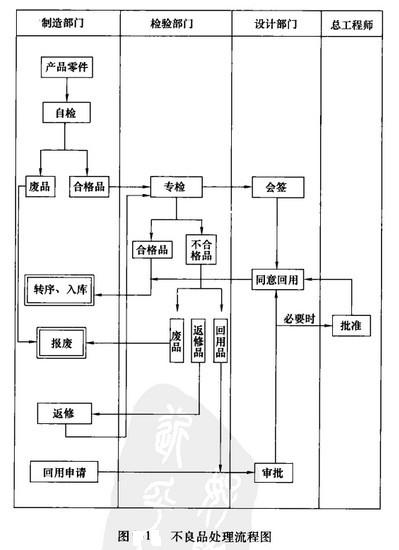
3.处置方法
对不良品的处置主要包括以下内容。
(1)纠正
纠正是指为消除已发现的不良品所采取的措施。纠正包括下列内容。
1)返工。对不良品采取措施,使其符合要求,成为良品。
2)降级。改变不良品的等级,使其符合不同于原来的要求。
3)报废。为避免不合格品原有的预期用途而采取的措施,如回收、销毁或是服务业中的中止服务。
(2)返修
返修是为使不良品满足预期用途而对其采取的措施。应注意,返修可能会改变芯片的某些部分,虽然能满足预期使用要求,但已不能称为良品,所有过程返工、返修后均应重检并记录,直至合格为止。
(3)纠正措施
纠正措施是为消除已经发现的不良品的原因所采取的措施。纠正措施与纠正不同,纠正是针对不良品的现象,目的是为了消除这种现象;而纠正措施是针对不良品的原因,目的是为了防止不良品的再次发生。例如一块电源板,发现一只电容器易坏,经过查找原因,发现是电容器的工作电压不够,于是,重新改变了电容器的技术要求,就不再出现上述情况了。这里更换电容器是纠正,而发现电容器的工作电压不够并改变要求就是纠正措施。纠正可以与纠正措施一起实施,这样既消除了不良品,又能防止不良品的再次发生。但应注意并非所有不良品均需采取纠正措施,应根据不良品发生的原因、频次、严重性程度来确定是否应该采取纠正措施。
纠正措施的实施过程包括确认出现的质量问题;职责分配;评价问题的严重性;分析产生问题的原因;制定防止问题发生的措施;实施所制定的措施;对纠正措施的效果进行验证;在证明纠正措施有效的情况下,进行永久性更改,包括对质量体系、产品规范、生产工艺和作业指导等方面的更改。
(4)预防措施
预防措施是指为消除潜在的不合格品的原因所采取的措施。它与纠正措施不同之处在于,采取预防措施时不合格品尚未出现,它是通过对检验结果、统计过程控制等质量信息的趋势分析或对以前类似情况的分析,识别出可能会出现的不合格情况。